FDMの充填構造に着目してコストダウン!
本記事の内容が当てはまる造形方式
- FDM
- FDMは唯一スパース構造(中空)にすることができる
3DPの造形コストは、材料使用量に依存します。図1(a)のようにFDMはリール状の樹脂を溶かしながら一層ずつ積層することで造形します。その際、FDMは少しの隙間であれば、図1(b)のようにブリッジ(橋)状に造形することができるため、造形面の下側に少しの隙間があいていても造形できます。このため、図2(a)のように、モデルの中身を全て埋めてに造形することも(ソリッド構造)、図2(b)上下の面と壁面以外の、造形物の内部を網目状に隙間を立たせて造形することもできます(スパース構造)。
こうすることで図2(a)よりも、図2(b)の方が材料使用量が少なくなるため、コストを削減することができます。
図1(a)下から1層ずつ積み上げる
図1(b)ブリッジ
図2(a)ソリッド構造
図2(b)スパース構造
- 中空にした際の強度に注意
材料使用量の点からスパース構造はコスト削減につながります。しかしスパース構造はソリッド構造にくらべて強度が低下する可能性があります。そのため、造形物の形状や要求に対して正しい選択をする必要があります。
基本的にモデル表面はかわらないため、強度を必要としないデザイン確認や、削りだしで作成されていた形状、肉厚の厚い部分があるような形状部品自体に厚みが十分にある場合は、中身がスパース構造に向いています。
しかし、モールド部品のような薄肉形状はスパース構造で造形しても隙間がほとんどできず、材料使用量もソリッド構造と比べて変わらないため、ソリッド構造が向いています。さらに、強度を求められる部品にはソリッド構造にすることで強度確保ができます。
- 強度確保しながらコスト削減できないのか?
一部のFDM3Dプリンターではスパース構造の形状を変更することができます。
図3にあるように、スパース構造をハニカム形状にすることで圧縮方向に強さを保ちながら、コスト削減を行うことができます。
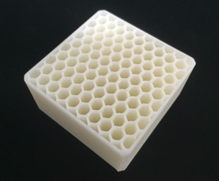
図3 ハニカム形状