- #コスト低減 #納期短縮
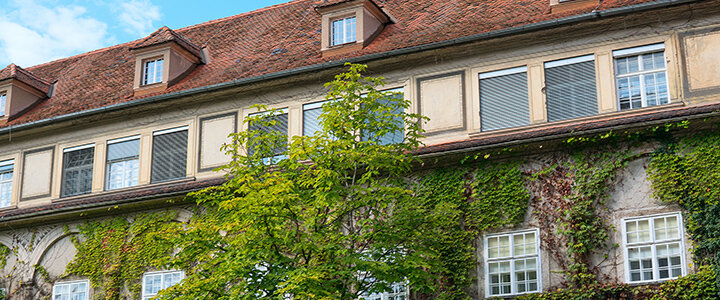
プロファイル
企業 | 住宅事業 |
---|---|
部門 | 設計・調達 |
活用状況 | 社内活用はほとんど実績がなかったとのこと。 |
事例概要
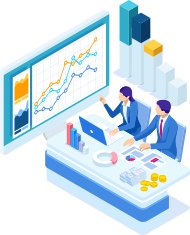
- 当該社は、窓のサッシ修繕を中心にマンションなどの集合住宅のリフォーム事業を手掛けています。
- 昨今、築30年を超えるストックマンションが増加する中、築年数からメーカーの補修サポートを受けられない、窓やサッシが多く存在しています。
- 本ケースでも、約40年前の部材で、補修品の入手が困難なドア部品の早期の交換要望でしたが、必要な数は100個程度で新たに金型を起こして製造するには、コストも納期も見合わない状況で、かつ「紙の図面」と「擦り減った現物」しかない状態でしたので、対応に大変苦慮しました。
- そのため発想を転換し、「3Dプリンター出力サービス」を活用し、紙の図面から3Dデータを新たに起こして3D造形を行うことで、小ロットの住宅パーツを僅か2週間で納品することができました。
従来はどんな課題があったのですか︖
40年前の部品がどうしても必要に。。
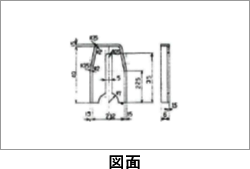
集合住宅のリフォーム事業を行う中で、既存部品を流用してコストを抑えるためという目的以外に、リフォーム対象の住戸の各部屋のスペックをそろえてリフォームしなければならないという制約事項が存在する場合があります。
昨今、築30年を超えるストックマンションが増加する中、築年数からメーカーの補修サポートを受けられない、窓やサッシが多く存在しており、住居者にとっても大きな問題になっています。
今回のドアの土台部品のケースも同様で、40年以上経った住宅部品の老朽化した窓サッシ部品の補修・改善が急遽発生。金型を起こして対応では仕様上もコスト上も、新規の部品に取り換えることが難しく、対応策を早期に決めなくてはいけませんでした。
図面データもない。対策は?
また、対応にあたって入手可能な情報は、"紙の図面"と"擦り減った現物"だけでした。さらに必要な数は少数で、せいぜいが数十個。また今後修繕対応が発生しても同じ製品である保証はありません。それでも金型を起こして対応するか、それ以外の方法はないのか、対応策を模索していました。
このような中、社内では対応が困難と判断して、外部の「3Dプリンター出力サービス」に相談した結果、3Dプリンターによる造形で課題解決ができると判断して、取り組みを進めました。
3Dプリンターでどのように課題を解決されましたか︖
損傷部品を同等材料で製造
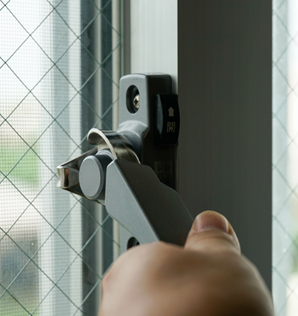
新築当時の納品図書に紙の図面があったため、損傷した部品と一緒に3Dプリンターでの造形が可能かご相談をいただきました。紙の図面からすぐに3Dモデルデータを起こし、現物を確認しながら材質を検討しました。
また、仕様とコストのバランスがとれる造形方法を検討し、ご提案。すぐにほしいという事でPA12(ポリアミド)で造形し、結果として100個の部材を2週間で納入することができました。
今回、3Dプリンターを活用することで、従来在庫の有る部品に近いコストで作製することができ、お客様の求める納期とコストで納品することが可能となりました。
3Dプリンター導⼊後の効果はいかがですか︖
ビンテージマンションで必要な部品をリーズナブルに造形できる。
新規にドアを交換するとなると、一か所10万円以上のコスト負担が発生する上に、廃材の廃棄コスト取替工数が発生します。今回のよう1一部品の交換だけで対応できればコストは大幅に削減でき、作業も簡易な作業に抑えることができますが、金型を起こしてしまうと時間もコストもかさんでいきます。また、その金型の保管や管理にかかる工数も積み上がっていきます。
今回は、3Dプリンターを活用することで、リフォーム部品100個を約2週間で造形し、単価を数千円レベルに抑えることができたので、大幅なリードタイム削減とコストダウンを実現できました。
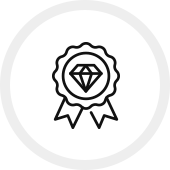
RESULT01
Qualityの改善
- 既存部品と同等品質の部品を3Dプリンターで造形
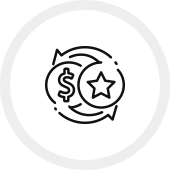
RESULT02
Costの改善
- 金型レスで初期費用を大幅に抑え、単価数千円レベルで調達
(従来方法での新規部品製造の場合、10万円以上のコストが発生)
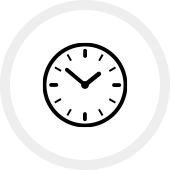
RESULT03
Deliveryの改善
- 3Dプリンター造形により約2週間で100個の部材をタイムリーに納品
- 解決した製品/サービスはこちら
-
-
豊富な保有設備と社内外の造形依頼に対応してきた経験を活かした造形サービスをおこなうリコーの3Dプリンター出力サービス。
造形サービス以外にも、プリプロセス(紙図面からの3DCADデータ起こし、ワークを3Dスキャニングし3Dデータ化するリバースエンジニアリングなど)や研磨などの後加工もワンストップで提供。 -
3種類の素材を同時噴射することで、複数の材料からなるパーツやアセンブリを単一の工程で造形することができます。複数の樹脂を組み合わせたデジタルマテリアルによって、より最終製品に近い質感や感触を持った造形物の出力が可能になることで、設計サイクルの初期段階であらゆる角度から製品を評価することができます。
-
Why RICOH
(リコーだからできる事)
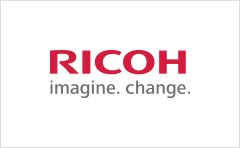
リコーは3Dプリンターをものづくりの現場で20年以上にわたって活用してきました。
製品の試作に始まり治具製造、さらには最終製品製造へと適用範囲を広げております。
2014年以降、自社で蓄積してきたノウハウを活かして
3Dプリンターの販売や3Dプリンター出力サービスを提供しております。
3Dプリンター出力サービスでは、お客様のご要望やご予算に合わせて
最適な造形材料・造形方式・後加工などをご提案しています。
従来の加工方法(切削/射出成型など)とは異なる、
3Dプリントの特性を最大限に活かした造形を丁寧にご支援します。