- #最終製品 #フルカラー #透明 #アクリル #ゴムライク
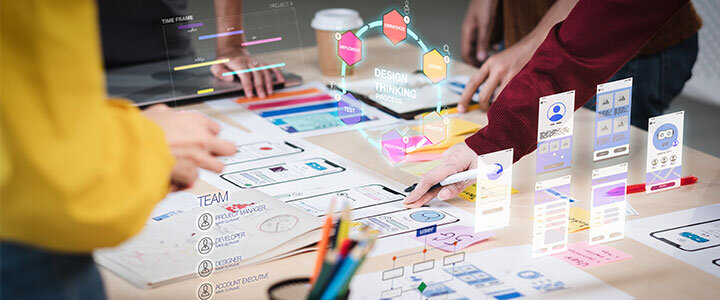
試作分野で3Dプリンターの有用性が認められ、多くの企業が製品開発に取り組む際に3Dプリンターを活用するようになってきました。では実際に、製品開発段階で活躍するデザイン会社や試作会社は現在どこまで3Dプリンターを活用しているのかが気になるところです。自動車業界をはじめ、ベンチャー企業などの製品開発も手掛けてきたデザイン・試作会社の一つ株式会社日南の工場、ショールームをご案内いただきながら、お話を伺いました。
語り手:株式会社日南 猿渡義市氏、野崎亮氏、渡辺俊幸氏
聞き手:3DPエキスパート編集部
目次
日南とは
株式会社日南は1970年創業の産業界のプロトタイプ製作を主幹事業として、製品開発にかかわるすべてのプロセスをフルパッケージでサポートする開発総合支援会社です。早くから3Dモデルや3Dプリンターを取り入れ、デジタルなモノづくりをメーカー各社とともに手掛けています。
日南のデザイン部門責任者の猿渡 義市氏
水循環型手洗いスタンドWOTA社の「WOSH」 の開発秘話
様々なプロダクト開発のお手伝いをされていると思うのですが、最近手掛けた事例を教えていただけますか?
猿渡氏:コロナ禍で大きく注目を集めた手洗いですが、自律分散型水循環システム の開発をしていたWOTA株式会社のお仕事をお手伝いしました。私たちはデザイン、プロトタイプの設計と製作、VR/ARの制作をお手伝いしています。大変興味深いプロジェクトではあったのですが、マーケティングの計画上、製作期間に時間がありませんでした。
掲載元:WOTA株式会社ホームページ
世界中どこにでもある規格化されたドラム缶を筐体に、3Dプリンターで造形したパーツを組み合わせることで、世界中どこでも手が洗える、公衆衛生を行動に落とし込める道具を作るというコンセプトを描き、理想を最短でどのように社会実装できるレベルに落とし込むかは、 非常にハードルの高いチャレンジでした。
手洗いという習慣のない海外の方は、見ただけで使い方が感じられるUI(User Interface)をどのように実現するべきか。時間は決まっている中で、できるかぎりコンセプトを製品に落とし込みたい。こうしたチャレンジは、時間との戦いです。
デジタルなモノづくりだからできたチャレンジとしてはどんなことがありますか?
猿渡氏:2つご紹介しましょう。一つは3Dモデルを使ったCGでの利用イメージの明確化、もう一つは3Dプリンターによる高速での試作です。
1点目の3Dモデルを使ったCGによる利用イメージの可視化ですが、WOSHは30秒間手を洗っている間にスマホもUV光で殺菌できるという機能を提供しています。世界ではいままで手洗い設備にアクセスすることが困難という人もいましたので、どの程度洗うのが衛生的に良いのか分かりません。
そこでWOSHは手を洗う時間が分かるように、洗浄ボウルの周りをLEDで光らせる設計にしました。
この際に、どのように光らせるかというが議論になりました。そこで最初にCGでアニメーションを作ることで、光が徐々に消えていくようにすることで手を洗っている時間を把握できる、この方がユーザー体験として提供したい方向だ、という形で関係者の意思統一が図れました。
左:3Dプリンターで一体造形したWOSHの部品。右:3つの部品に分割した量産部品
2点目の3Dプリンターによる高速での試作なのですが、プロトタイプ製作において、多くのパーツは3Dプリンターで試作を行いました。
この部品を見ていただきたいのですが、両手で持たなければいけないくらい大きい部品です。実際に水がながれる流路として使われる部品なのですが、試作段階では本来20を超えるパーツを1パーツで造形しました。かなり複雑な形状だと思います。
また3Dプリンターらしい機能性も実現したいということで、金型を起こして射出成型する場合ではできない斜めの流路などに取り組んでいます。量産時は金型を使った生産になるということで、設計変更をおこなったのですが、その変更でもかなり攻めた設計になっています。
どうしても金型では実現できない箇所は修正していますが、なるべく試作時の基本形を崩さずに3つの部品にわけて成型するというチャレンジになっています。
Stratasys J850が2機、Stratasys Fortus 400 が1機など複数の3Dプリンターが稼働。ブラスト装置なども備えすぐに使える部品を用意する体制を実現している
旧車のエアコン吹き出し口を3Dプリンターで造形。ワンパーツで稼働部を造形する工夫
試作以外にも3Dプリンターを活用しているシーンはありますか?
猿渡氏:はい。実際に最終部品として3Dプリンター製の部品を自動車の部品として利用している事例をご紹介します。
私たちは発売から数十年経った自動車のレストモッドにも取り組んでいます。レストモッドというのは、ただ単純に美しくするだけではなく、オリジナルのデザインを損ねることなく最新のテクノロジーをインストールし、ストレスのないカーライフを楽しむためのカスタムです。
たとえばメルセデスベンツの中でも人気の高いGクラスの前身「ゲレンデヴァーゲン」のオーナーさんの中には、もう数十年愛着を持って乗り続けている方もいらっしゃいます。使い慣れた愛着のある車だけど、古くなれば性能も相対的に見劣りしていきます。
そういった場合にレストモッドが活用できます。例えば、エンジンとミッションを現代のモノにスワップして、 性能面を強化していきます。その際に、ミッションを4速から6速に仕様変更した場合、シフトノブのデザインにもこだわりたいところです。
今回の場合、4速のシフトノブをスキャンしてデータを起こし、6速のシフトノブを新しく製作しました。当時の雰囲気を活かしたデザインで、現代の機能に満たした部品を新しく作っています。
6速にレストモッドしたゲレンデヴァーゲンのシフトノブ
同じような取り組みは、他にもあります。エアコンがついていない車にエアコンを設置するため吹き出し口を増設するという取り組みです。
設置した場所は1DINのカセットユニット が設置してあった場所です。現在の生活ではカセットで音楽を聴くことはなくなりました。その スペースにピッタリはまるエアコンの吹き出し口をゼロからデザインし、3Dプリンターで造形しました。
この3Dプリンターで造形したエアコンの吹き出し口は複数の可動部分も含めて1パーツで造形しています。組み立てしていないわけです。3Dプリンターであれば稼働部分を持つパーツも1度の造形で一台の3Dプリンターで造形できます。金型も不要です。データから直接造形できます。
使ってみて実際に造形してみて、期待通りに動くか検証します。
エアコンの吹き出し口。上下左右に稼働するが1つの部品として一体造形されている
このエアコンの吹き出し口部分は、上下左右に稼働する部分は稼働するので、スムーズに動かしたいところです。硬すぎて使えないとか、緩すぎて、丁度よい場所に風を向けられないことがないように、強度を保って位置を調整できる必要があります。
またぎこちなく動くのではなく、新車のようにスムーズに動かせるようになっていないと使い勝手が悪いわけです。実際に何度か造形しながら使い心地を試しながら改良を加えていきました。
最終的に、稼働する部分の軸はゴムライク樹脂を使用し、強度が求められる場所と材料を変えています。
またABSを混ぜると仕上がりが悪くなったため、材料の配合も変えています。J850 はこうした材料配分を変えながらマルチマテリアルで造形 ができますので、何度も作り直しながら最適な品質を追求していきました 。
また表面のシボパターンもサブスタンスペイントというソフトウェアを活用して3Dデータ化してプリントしています。
「夜に造形指示を出せば翌日にはモノができている。試行錯誤して設計を煮詰めていけるのが3Dプリンターの魅力」(渡辺氏)
渡辺氏:時間をかけて造形してもサポート材をとる際に破損してしまうケースもありました。
私たちは試行錯誤を重ね、稼働する部分を包むゲル状のサポート材が抜けやすいように接合部に穴を設けて薬品を利用してゆっくり洗いながら化石を発掘するようにサポート材を除去するなど、その都度造形しながら最適な方法を考えだし、実行に移していくことで従来にない造形を可能にしてきました。
左右に動くルーバーと上下に動く枠を一体で成型するために設計面ではかなり難易度が高かったのですが、何度も実際に造形し、動き方を見ながら改修していくことで期待通りの仕上がりに収めることができました。
取り組みを通じてノウハウが蓄積される。使いこなす姿勢が成果につながる。
イメージを広げるための造形サンプル
渡辺氏:今ある装置でこんなことができるというのを一つ一つ私たち自身で確かめていきながら、実現できる幅を広げています。
3Dプリンターの進化は驚くほど進んでいますが、装置ができることをまず使う側が知る必要があります。
例えばストラタシス社製の3DプリンターJ850では様々な色彩や質感が表現できるのですが、実際に出力してみた見本帳のようなものを作ろうとしています。多彩なシボや透明部品にも素早く高い品質で対応できることも見せられますし、そこからお客様のアイデア発掘ができればと思い、いろいろなバリエーションを造形しているところです。
野崎氏:見る方向が変わると色が変わるこの出力サンプルは、ネットで話題になっていたものを見かけて、試行錯誤しながら作りました。他にも、透明部品、カーボン柄の仕上げなど実際に造形していますので、実際に手で触れて目で見ていただきたいと思います。
多くの3Dプリンター造形サンプルが並ぶ展示コーナー
3Dプリンターで何でも造形するわけではない。便利な道具として使いこなす姿勢
「限られた検討時間の中でも、より良いものを作り出せるところが3Dプリンターの本当の価値」(野崎氏)
日南さんでは3Dプリンターを活用して多くのモノづくりがすでに進行していると思うのですが、どんな点にメリットがあるとお考えですか?また逆に使っていて大変な点は何ですか?
野崎氏:3Dプリンターは一度ノウハウを確立してしまえば、加工中に人が張り付かなくても、帰宅前にボタンを押して朝にモノが仕上がってくる便利さがあります。しかし使いこなすのはトライアンドエラーを多く繰り返し、経験とノウハウが必要です。こうしたメリットやデメリットはやはり実際に使っていないと実感できないところもあります。
私はもともと金型が専門なのですが、渡辺のようにデータづくりに従事してきた社員など、猿渡の指揮の下、各部署からクロスファンクショナルチームがアサインされ、取り組んできました。例えば射出成型用の金型では必要だったことが3Dプリンターで造形する際には制約条件にならないなど、既存工法ではできなかったことに従来工法でものを創ってきた人間が取り組んでいます。
実際に触ってみないと分からないことは沢山あります。なんでも3Dプリンターで対応するべきではない場合もあります。3Dプリンターでやる必要のないことは最適な他の工法で実現すればよいと思います。逆に3Dプリンターでしかできないと感じるチャレンジも多く存在します。
材料代は高いのですが、それ以上に価値があると思うのです。こうした価値ある分野で、限られた検討時間の中でも、より良いものを作り出せるところが3Dプリンターの本当の価値だと思います。今後も装置が進化してより強度の高い、より精度の高い部品が作れるようになると思います。私たちは単純にもらったデータを形にするだけではなく、その中で改善を行いより作りたかったものを具現化することに価値を感じていただきたいと思っています。
実際にJ850で造形された部品をみながら設計の苦労を振り返る
装置は日進月歩。どうすれば先進企業のように使いこなせるのか
表現力が上がり複数の部品を違う仕上げで造形できるStratasys J850は自動車業界をはじめ、幅広い業界でのデザインを具現化してきた日南でほぼ毎日稼働しているということです。
実際に旧車の部品として利用している部品もあるとのことで、その活用の幅は試作領域に留まりませんでした。
世界では先進的な多くの3Dプリンター活用事例がでてきていますが、日本でもこうした先進企業の旺盛な取り組みが広がっています。どうすれば先進企業のように業務に組み込み活用を図っていくことができるのか、いまこの現場で何ができるかが課題になっているケースも多くあります。各社各現場で状況は異なるので、答えは一様ではありませんが、3Dプリンターを上手く活用できる現実的な取り組み方を考えていく必要があります。
3Dプリンターの活用について
リコージャパンでは先進企業のように3Dプリンターを活用したというご相談にも、リコーグループが3Dプリンターを活用してきた経験を踏まえた上でご提案しています。
「こんなものを作りたい!」「3Dプリンターでどうにかできないか?」というご相談、お客様の課題に即した3Dプリンター機種のご紹介をしております。
また3Dプリンター出力サービスでは、専任の技術者がお客様の作りたいもの、ご希望に合わせて最適な造形方式、造形材料、後加工までご提案させて頂きます。
ご興味のある方は以下のお問い合わせフォームからお気軽にご相談ください。
ライタープロフィール
3Dプリンターのポータルサイト、シェアラボニュースの編集長として、これまで200人以上の業界関係者にインタヴューを実施。3DPエキスパート編集部ではライターとして取材・記事制作を担当。
Why RICOH
(リコーだからできる事)
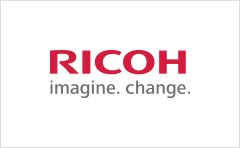
リコーは3Dプリンターをものづくりの現場で20年以上にわたって活用してきました。
製品の試作に始まり治具製造、さらには最終製品製造へと適用範囲を広げております。
2014年以降、自社で蓄積してきたノウハウを活かして
3Dプリンターの販売や3Dプリンター出力サービスを提供しております。
3Dプリンター出力サービスでは、お客様のご要望やご予算に合わせて
最適な造形材料・造形方式・後加工などをご提案しています。
従来の加工方法(切削/射出成型など)とは異なる、
3Dプリントの特性を最大限に活かした造形を丁寧にご支援します。