- #コスト低減 #納期短縮 #PA12
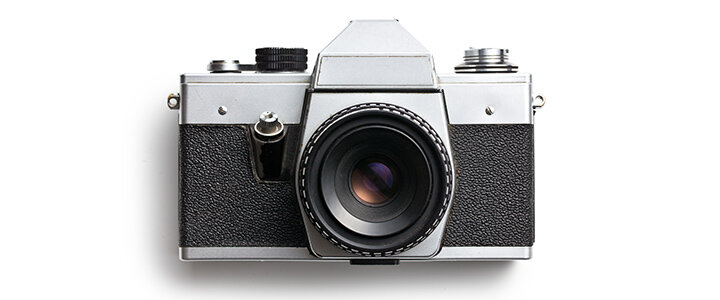
プロファイル
企業 | リコー |
---|---|
部門 | カメラ |
活用状況 | 試作品に活用する一方で社外にサービスビューロとして造形サービスを提供するスペシャリスト |
事例概要
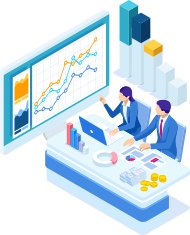
- 需要予測が外れて、保守部品の増産が必要になったものの、金型を破棄していたため、対応に苦慮していました。
- 保守部品はPC(ポリカーボネイト)を射出成型したものでしたが、PA12への材質置換でも検査水準を満たせることが判明したため、直接3Dプリンターで保守部品を造形することで、大幅なコスト削減を実現しました。
従来はどんな課題があったのですか?
需要予測外の保守部品需要が発生
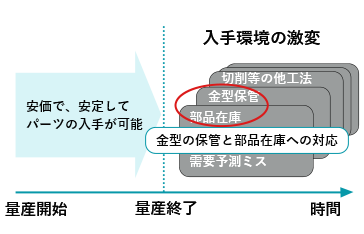
生産終了となったデジタルカメラのある機種において、事前の予測を超える保守部品の需要があったため、在庫が急速に減ってしまい、追加生産が必要になってしまいました。
しかしすでに金型は破棄しており、メーカーとして保証している部品対応期間は残りわずかという中で、新規に金型を製作することはできれば避けたい状況でした。
3Dプリンターでどのように課題を解決されましたか︖
材質置換を行い、社内試験
保守部品はPCを射出成形して作られていましたが、3Dモデルが社内に存在したため、3Dプリンターでの造形にトライ。PA12に材料置換を行い、社内基準を満たせる性能をもっているか試験を行うことにしました。
社内試験に合格!大幅コスト削減を実現
3Dプリンターで造形された部品を塗装し、社内規定の試験工程で従来品と同等の検査を行いました。その結果、問題なく社内検査に合格し、品質上問題ないことが確認できました。
3Dプリンター導⼊後の効果はいかがですか︖
金型補修以外に、データから直接製造するという打ち手を獲得。
調達戦略に幅が生まれた。
コストと納期を大幅に短縮し、必要な際に必要な分だけサービスパーツを補充できる実績を作る事ができました。該当するパーツは製品全体から見ると一部分でしかありませんが、材料置換ができれば、大きなコストメリットを品質基準を変えることなく実現できることが実証できました。
すべてのパーツに適応できるわけではありませんが、社内実績は次の挑戦を可能にするきっかけになります。今後のMRO部品調達戦略に大きな幅が生まれた瞬間だったといえるでしょう。
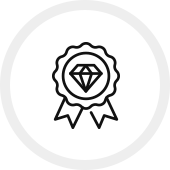
RESULT01
Qualityの改善
- 材料置換したが、既存品の社内試験を合格
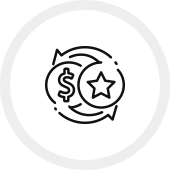
RESULT02
Costの改善
- 金型レスで調達できた為、初期費用を大幅に削減できた。
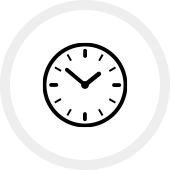
RESULT03
Deliveryの改善
- 直接製造で小ロットのオンデマンド生産体制を確立。
- 解決した製品/サービスはこちら
-
-
豊富な保有設備と社内外の造形依頼に対応してきた経験を活かした造形サービスをおこなうリコーの3Dプリンター出力サービス。
造形サービス以外にも、プリプロセス(紙図面からの3DCADデータ起こし、ワークを3Dスキャニングし3Dデータ化するリバースエンジニアリングなど)や研磨などの後加工もワンストップで提供。 -
3種類の素材を同時噴射することで、複数の材料からなるパーツやアセンブリを単一の工程で造形することができます。複数の樹脂を組み合わせたデジタルマテリアルによって、より最終製品に近い質感や感触を持った造形物の出力が可能になることで、設計サイクルの初期段階であらゆる角度から製品を評価することができます。
-
Why RICOH
(リコーだからできる事)
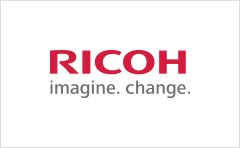
リコーは3Dプリンターをものづくりの現場で20年以上にわたって活用してきました。
製品の試作に始まり治具製造、さらには最終製品製造へと適用範囲を広げております。
2014年以降、自社で蓄積してきたノウハウを活かして
3Dプリンターの販売や3Dプリンター出力サービスを提供しております。
3Dプリンター出力サービスでは、お客様のご要望やご予算に合わせて
最適な造形材料・造形方式・後加工などをご提案しています。
従来の加工方法(切削/射出成型など)とは異なる、
3Dプリントの特性を最大限に活かした造形を丁寧にご支援します。