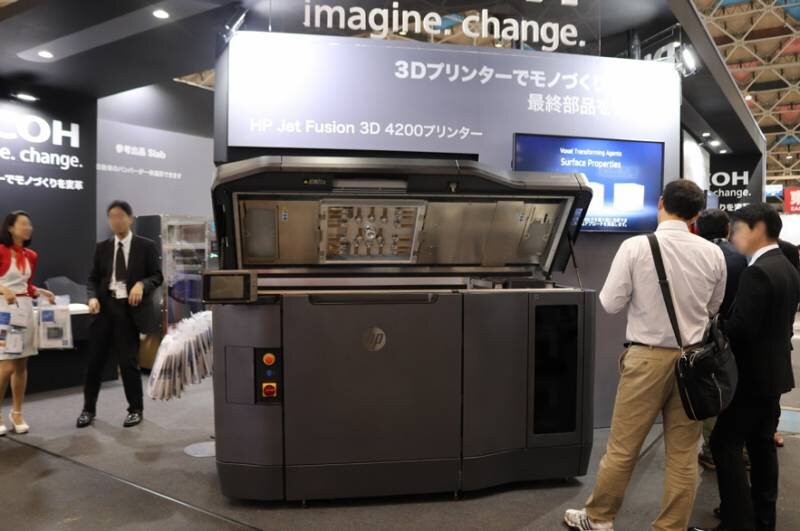
グローバル社会が加速する現在、国際競争力の向上や、ユーザーのニーズに対応するため、製造分野だけでなく、設計・試作の分野にも低コスト・高効率化を求める動きが強まっています。さらに近年は顧客ニーズの多様化も加速しています。そのため製造の現場では従来のような小品種大量生産から、多品種少量生産が求められるようになっています。開発の速さと信頼性、品種の多さと低コスト。相反するものが求められる現在、製品開発の現場には何が必要になるのか。名古屋で行われた設計・製造ソリューション展からその答えを探ります。
設計・製造ソリューション展とは
設計・製造ソリューション展は、2018年4月11日~13日に名古屋ポートメッセで開催された「名古屋ものづくりワールド」の1つとして開催されました。会場となった名古屋ポートメッセは名古屋駅から南におよそ15km。名古屋港の入り口にあたる、金城ふ頭に位置しています。鉄鋼材料や小麦、自動車などを積んだ船が行き交う、いわば中部地区の経済の要ともいえる場所です。会場では、設計・製造ソリューション展の他に、機械要素技術展、航空・宇宙機器開発展、工場・設備備品展の合計4つの展示会が同時開催され、会期である3日間の間に1140社が出展、3万5千人の来場者が訪れました。世界最大級の「ものづくり専門展」といっていいでしょう。
低コスト・高効率な製品開発の担い手、3Dプリンターブースの紹介
3Dプリンターは低コスト・高効率な製品開発の手段の1つです。日本に先駆けて欧米などではすでに開発の現場で活用される場面も急速に増えてきているといいます。設計・製造ソリューション展の中でも3Dプリンターゾーンは、CAD/CAMゾーンに次ぐ2番目に大きなゾーンであり、出展企業の多さからも関心の高さをうかがい知ることができました。
ここでは3Dプリンターで出展していた企業をいくつか紹介したいと思います。
リコージャパン
リコージャパンが打ち出すのは、『最終部品を3Dプリンターで作る』と『高機能試作を3Dプリンターで作る』の2つの大きなテーマです。
『最終部品を3Dプリンターで作る』は、HP Jet Fusion 3Dプリンターをメインにお客様事例を交えて紹介。『高機能試作を3Dプリンターで作る』は、envisionTECをメインに他の方式と比較しながら、その高精細を紹介しています。
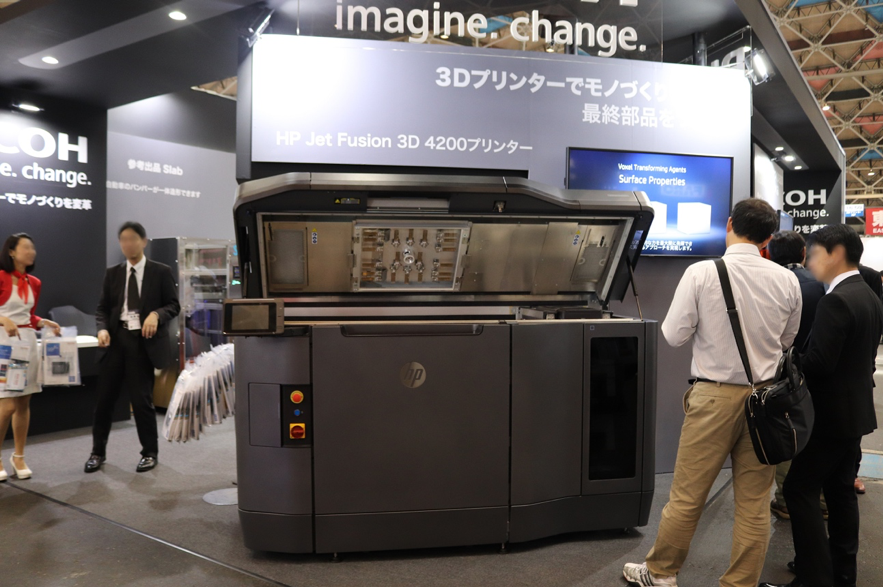
HP Jet Fusion 3D 4200
その生産速度、従来の10倍。HP Jet Fusion 3D 4200
3Dプリンターで最終製品を造形する場合は樹脂の粉末にレーザーを照射し、その部分の樹脂を溶かして固める手法が主流でした。しかしその方式において最大の課題となっていたのは造形の速さです。HP Jet Fusionではレーザーを照射するのではなく、ハロゲンライトの照射により樹脂粉末を硬化させます。紙に印刷するインクジェットプリンターと同様、黒いインク(フュージングエージェント)を樹脂粉末に噴射。そこにハロゲンライトを照射することにより、フュージングエージェントが噴射された部分のみが硬化するのです。これにより従来のレーザー式の3Dプリンターに比べ3倍早い造形を可能にしました。さらにHP Jet Fusionでは造形材料のセットや造形物の取り出しにおいて、資源的にも時間的にも効率的なフローを確立。結果として従来の10倍早い造形を可能にしました。
HP Jet Fusionの特長は造形のスピードが早いだけではありません。生産性の高さもまたHP Jet Fusionの大きな特長なのです。
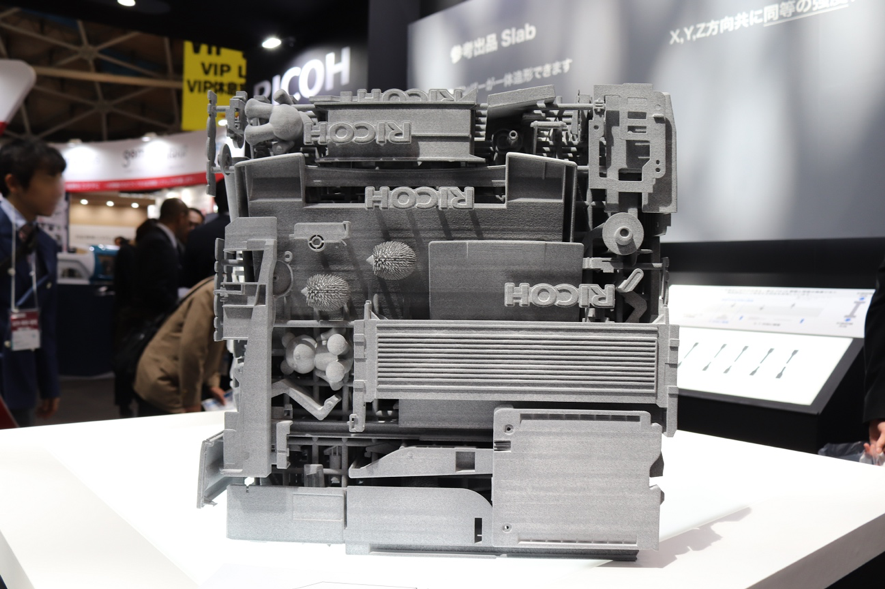
380mm✕380mmの中で効率的に配置される部品
HP Jet Fusionのもうひとつの大きな特徴は造形物配置の最適化です。3Dプリンター造形の生産性を高めるために欠かすことができない要素の1つに、1回の造形にどれだけの部品を詰め込めるかという課題があります。1回の造形でできるだけ多くの部品を作ったほうが高効率なのは明白です。しかし造形の精度が悪ければ、部品と部品の小さな隙間が上手く分離できず、隣り合った部品同士がつながってしまうような不具合を引き起こします。しかしHP Jet Fusionならば精密な造形が可能なため、そのような不具合はありません。そして、1回の造形における最大サイズの380mm立方の中で、充填率「20%」を実現しました。
精密な造形が可能にするのは、高効率の造形だけではありません。薄肉成形や複雑なアンダー形状など、従来の金型を用いた射出成形では不可能だった形状を作ることもできます。
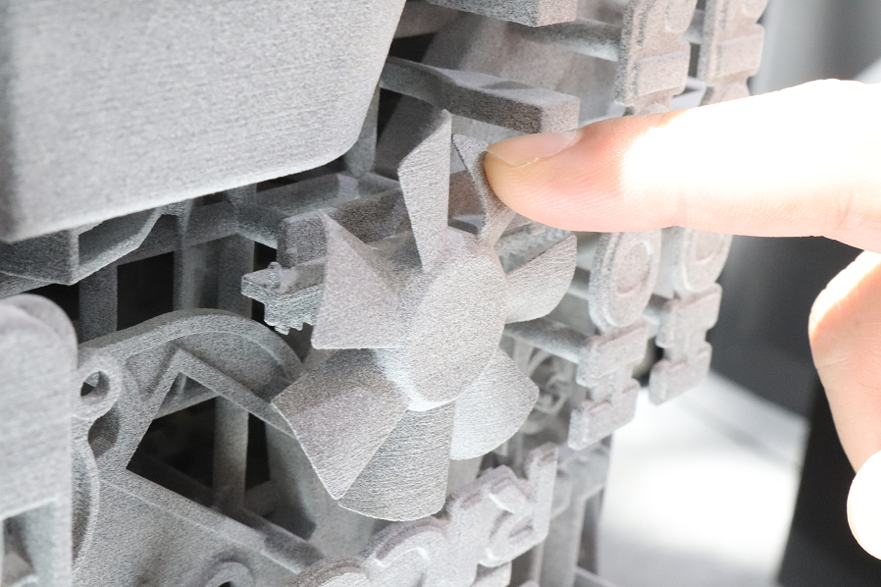
指で軽く押してたわむほどの薄肉パーツも造形
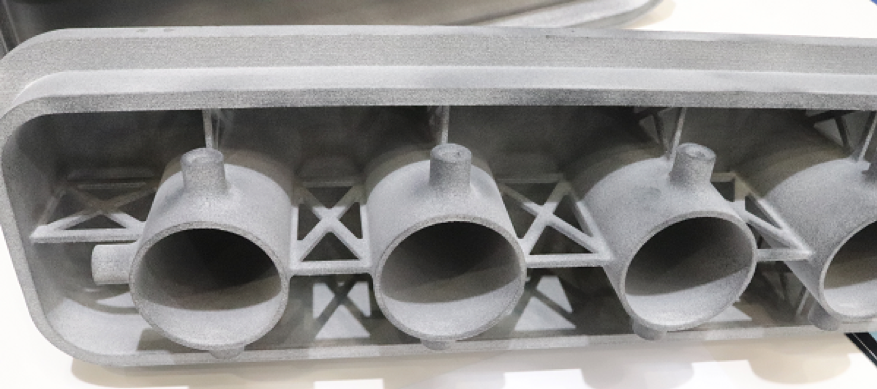
複雑なアンダー形状。このようなパーツも、一体成型で作ることができる
HP Jet Fusionを利用するメリットは、造形の速さや生産性の高さだけにとどまりません。最大の特徴は、最終部品として使用することに耐えうる強度があることです。
事実、HP Jet Fusionでは同機で造形した部品を製品の一部として使用しているそうです。今は限られた数のみの使用に留まっていますが、将来的には50部品ほどを同機製にすることを目指しているということです。
最小積層ピッチ0.025mm。Perfactory 4 LED standard XL
リコージャパンが取り扱う3DプリンターにはHP Jet Fusionよりもさらに高精度を誇るものもあります。それがPerfactory 4 LED standard XLです。特長は何といってもその精度の高さにあります。最小積層ピッチは0.025mm、平面では0.1mm単位の解像度を誇ります。Perfactory 4 LEDは元々、ジュエリーの原型用として使用されることが多かったのですが、リコージャパンではこれを工業用として提供することに成功しました。高い精度を生かし、可視化試験用の部品や電気のコネクターなど、製品としてそのまま使用することができる部品を造形しています。
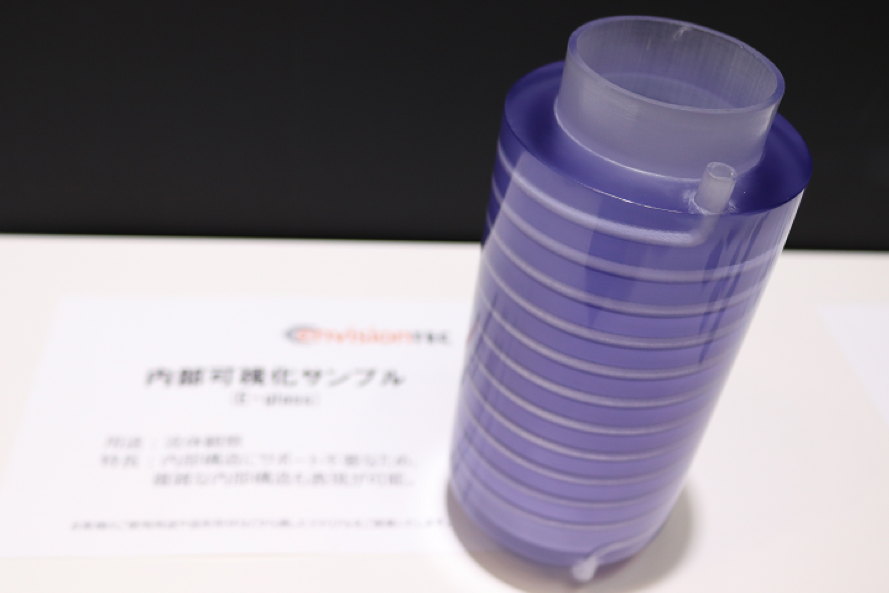
射出成形では成し得ない中空形状
溶かして積層する。Slab GEM444
リコージャパンでは他にも様々な種類の3Dプリンターを使用したソリューションを提供しています。ここでは参考出展されていたSlab GEM444を紹介します。
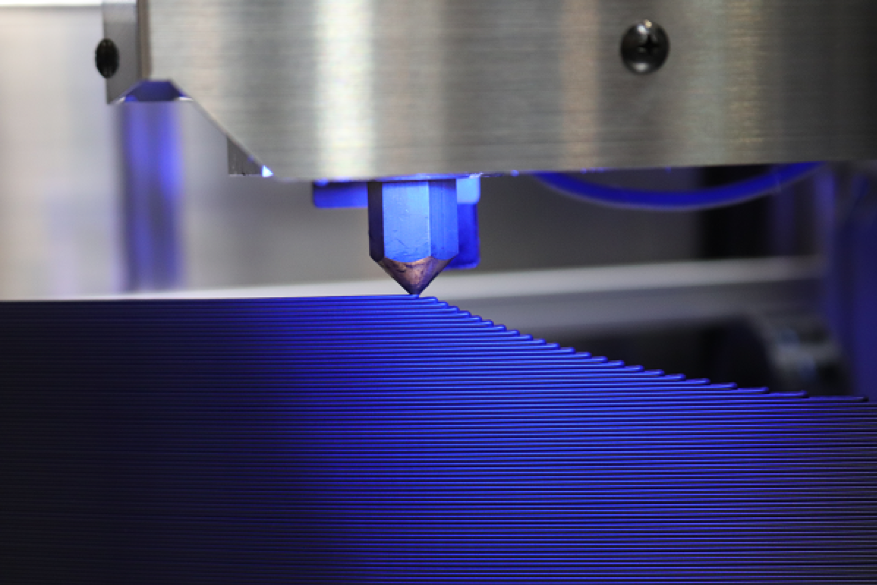
Slab GEM444積層の様子。中央のノズルの先端から溶けた樹脂が押し出される
Slabの特徴は射出成形用のペレットを溶かし、ノズルから押出しながら積層していくところにあります。これにより金型を必要とすることなく、大きなものを造形することができるのです。通常の射出成形の場合、大きな部品を作るためにはそれだけ大きな金型を試作段階から用意する必要があり、そのコストも金型の製作期間も膨大なものとなります。しかしSlabならば金型を必要とせず、大きな部品も手軽に造形することができるのです。現在は、造形後に表面を磨いて整えてから評価に進むほか、車の内装部品のような強度を必要としない部品としての実用化を狙う研究がすすめられています。
「3Dプリンターで作れるものは増えていますし、今後もさらに増えていくでしょう」とリコーの担当者は言います。例えば生産が終了してしまったサービスパーツなどの分野で、現在すでに3Dプリンターでの造形品が顧客の手元に届くケースも増えています。今後はオリジナリティを求める車のカスタムパーツや身体に合わせた自転車のサドル。さらに福祉的分野として義手や装具への展開も増えていくと考え、リコーではそれらに向けた造形技術やソリューションの開発を進めているとのことです。
専門の技術者が行う出力サービス
リコーが所有する高性能の3Dプリンターを駆使し、企業や大学などが求めるパーツを造形してくれるサービスです。もちろんサービスはそれだけではありません。専門の技術者が希望の形状を3Dプリンターで造形する上での課題解決をサポートしてくれるのです。これにより高性能な3Dプリンターを所持していない企業でも、高品質な3Dプリント製品を手にすることができるのです。
ストラタシス・ジャパン社
ストラタシス・ジャパン社は3Dプリンターメーカーとして、3Dプリンターが提供できる様々な製品を展示していました。
金型を樹脂型に。3Dプリンターで型を作る
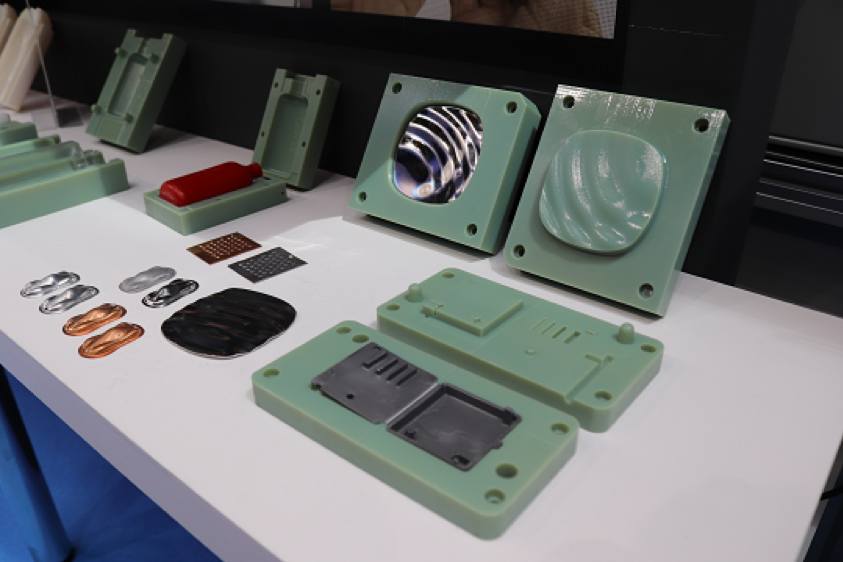
3Dプリンターで成形された型
ストラタシス・ジャパン社が提供する先進的なソリューションの1つが、射出成形やプレス成形に使用する型を3Dプリンターによって製作する方法です。ストラタシス・ジャパン社ではデジタルABSという独自の材料で、熱や圧力、摩耗に耐えうる型の製作を実現。これにより、従来は金属を使っていた型を3Dプリンターによる樹脂材料で製作することに成功したのです。樹脂の型と聞くと、型の強度を心配する人も多いかもしれません。しかしこれらの型は、試作用などに向けた数100台程度の小ロットの生産はもちろん、成形条件にもよりますが37,000台を超えるような生産にも耐えうるとのこと。本格的な大量生産を行う場合のコストメリットでは金型に軍配が上がりますが、少量多品種の生産や試作品の生産では3Dプリントの樹脂型に軍配が上がることでしょう。
3Dプリントによる樹脂型のメリットは、型のコスト低減や製作期間の短縮だけではありません。3Dデータさえあれば、いつでも好きなときに型を製作できるため、サービスパーツ用などとしてメーカーで長期間金型を保管する必要がなくなるのです。さらにサービスパーツなどを作る場合、材料は各メーカーがそれぞれに持っているものをそのまま使うことができます。3Dプリンター用の専用素材を使う必要がなく、そのため材料認証のような煩雑な手続きも必要ありません。また実際の製品と同じ試作品が手軽に作れるため、より信頼性の高い強度試験も可能になります。
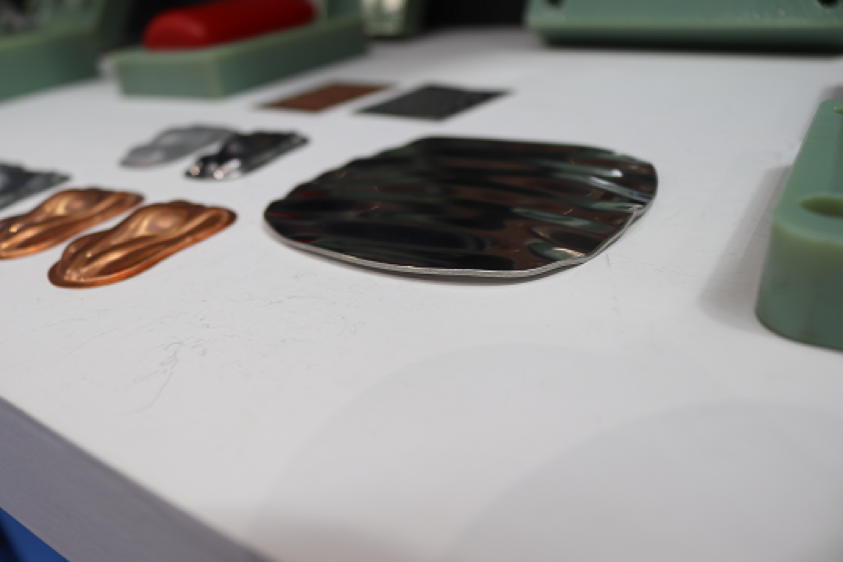
厚みを持った金属のプレスも可能だ
金属のプレス金型としては、このようなかなり厚みのある金属のプレスも可能です。さらに金型と違い型の素材そのものに潤滑作用があるため、プレスの際に潤滑油を必要としません。このため製品の脱脂工程を省くことができるという特長もあります。
少量多品種に適応するソリューション
ストラタシス・ジャパン社では型以外にも様々な分野でのソリューションを提供しています。その1つが自動車産業における3Dプリンター活用です。
例えば自動車工場で車の正面にエンブレムを取り付ける治具を挙げてみましょう。
従来はこのような金属製の治具が使われていました。
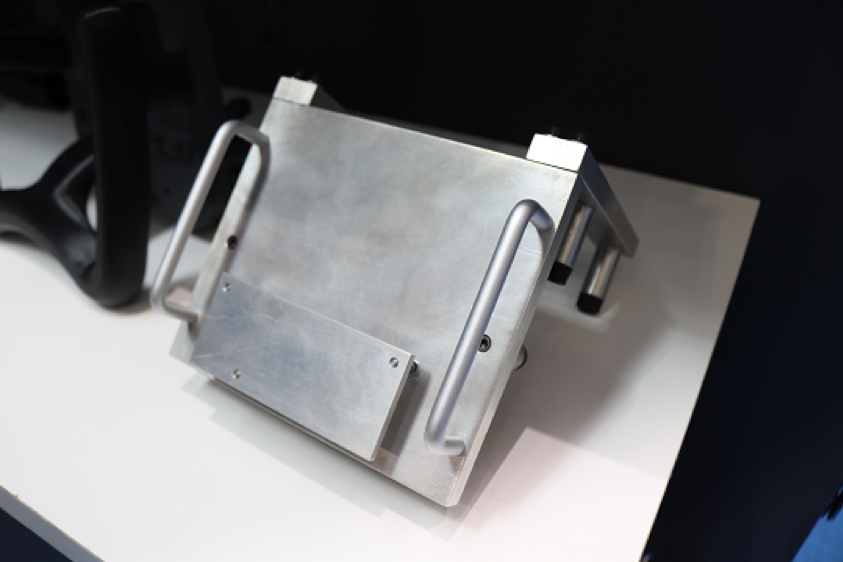
金属製の治具。重く直線的な形状で扱いにくい
金属の板やパーツを組み合わせて作られた治具は作るときには手軽ですが、重くて取り扱いにくいのが難点でした。しかしストラタス・ジャパン社が3Dプリンターで製作した樹脂製の治具はこのようになります。
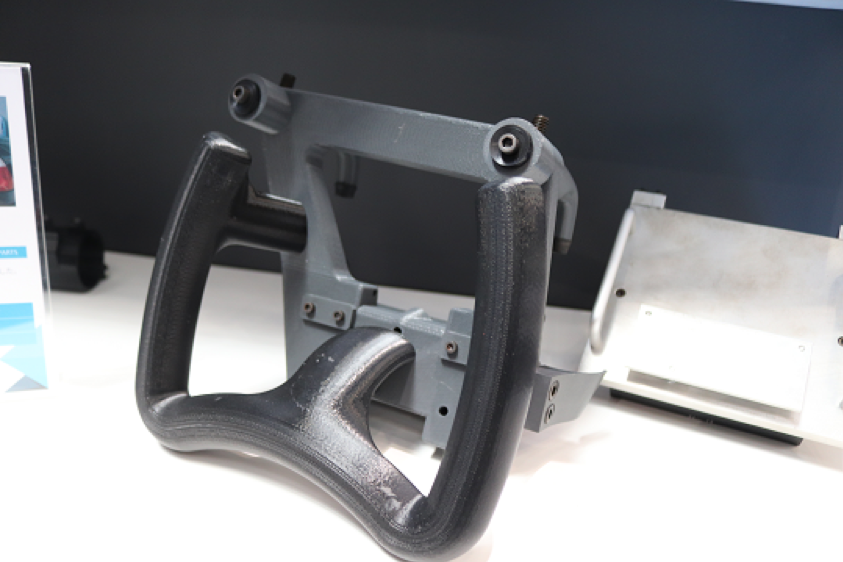
樹脂製の治具。軽くて人間工学的にもフィットする形状だ
材質が樹脂になったことで治具が軽くなり扱いやすくなりました。また3Dプリンターでなめらかな曲線を表現しているため人間工学的にも使用者の身体にフィットし、長い時間の作業でも疲れにくいという効果もあります。さらに治具が樹脂になったことで、治具が触れた拍子に車のボディーを傷つけてしまうリスクも激減しました。
その他の自動車産業分野での3Dプリンター活用例としては、テールライトやヘッドライトカバーのカットデザインの試作、バンパーの試作などもあります。
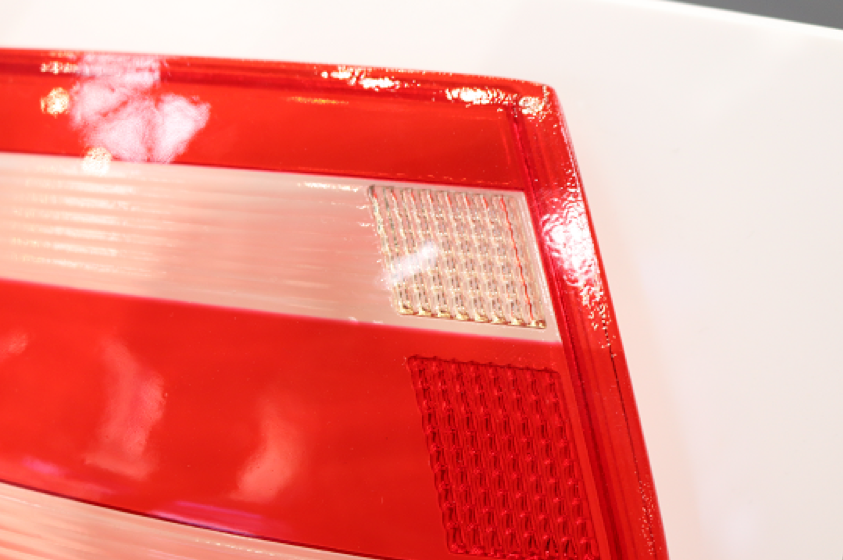
テールライトカットデザインの試作
ディーメック社
ディーメック社は自社開発の超高精細光造形3DプリンターACCULAS®シリーズ、および2種の新しい材料を提案します。
ACCULAS®シリーズの特長は何といっても大型造形が可能で且つ精密な造形にあります。最大造形サイズは850×650×500で高い形状表現性で微細造形にも適しています。
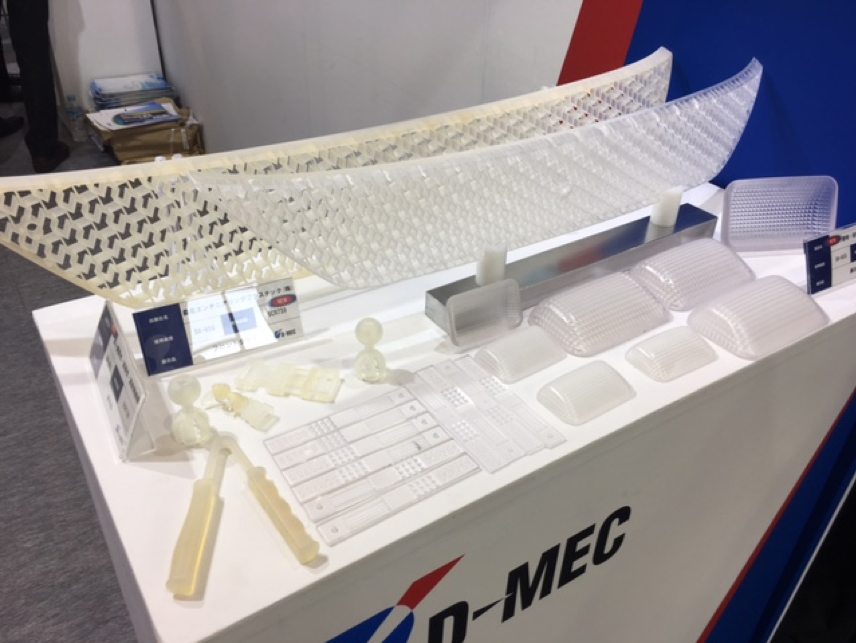
ディーメック社が提案する光造形3Dプリンター用の新樹脂SCR-739とSCR-876
SCR-739はこれまでにない高い靭性を持っています。10mmの厚さのSCR-739で造形した試験片に荷重を加え20%のひずみを与えても破壊しません。ABSと同様の白化現象が起こるにとどまります。従来光造形の樹脂というと脆く、壊れやすいというイメージでしたが、それを大きく覆す材料なのです。靭性が高いため、薄肉板のモデルやクリップのモデルなどの造形をすることも可能です。
一方SCR-876の特長は透明であること、そして熱に強いことが挙げられます。SCR-876はABSとほぼ同等の、100℃を超える熱に耐えることが可能です。さらに透明である性質を生かし、照明パネルなどのモデリング、ドライヤーの透明カバーなどの試作に使用することができます。
その他メーカーによる3Dプリンターのソリューション展開
3Dプリンターを軸に各社が提供するソリューションは多岐にわたります。ここでは精度や高機能な材料を提案するその他企業や、注目すべきソリューションを紹介していきます。
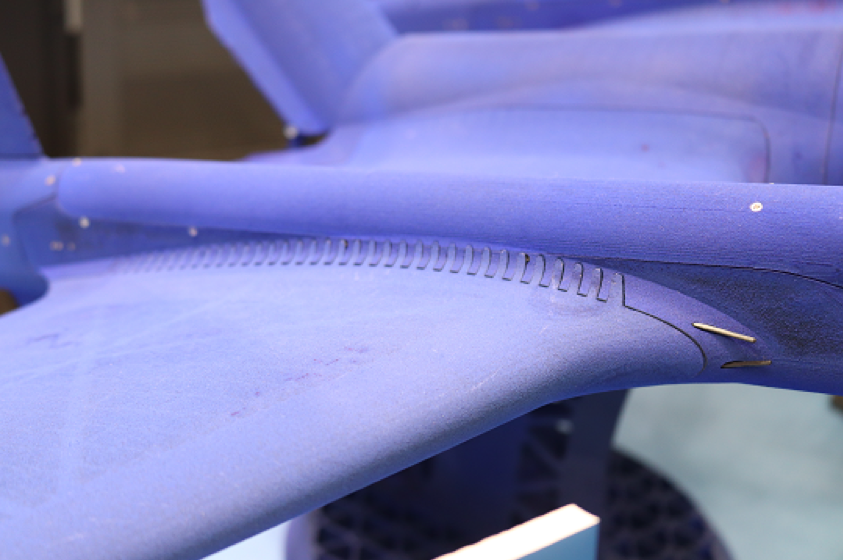
後処理なしで精密に噛み合う造形品。精度の良さをアピールする企業も多い
面精度の高さをアピールする企業もあります。写真は九州大学との共同研究のために製作された飛行機の翼と胴体の接合部です。ラックのような形状の2パーツが、後処理なしで見事に噛み合っています。
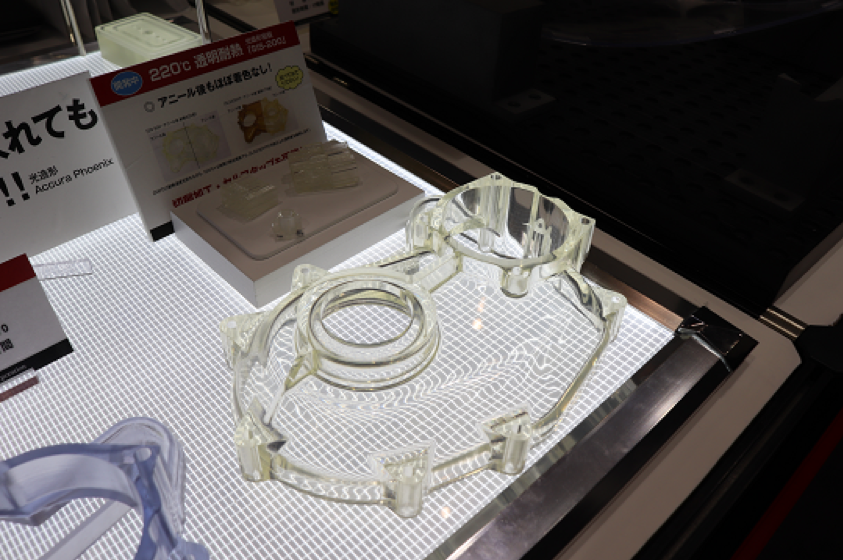
材料分野の発展もめざましい
高機能な材料をアピールする企業もあります。写真はプラスチックですが220℃まで対応できるという素材。自動車のトランスミッションのモデルを製作し、油の流れを可視化することができるといいます。トランスミッションの油の流れの確認は、現在シミュレーションが主流ですが、やはり現物で見てみないと分からないケースも存在するようです。条件を設定しきれない、複雑な事象の解明などに役に立ちそうです。
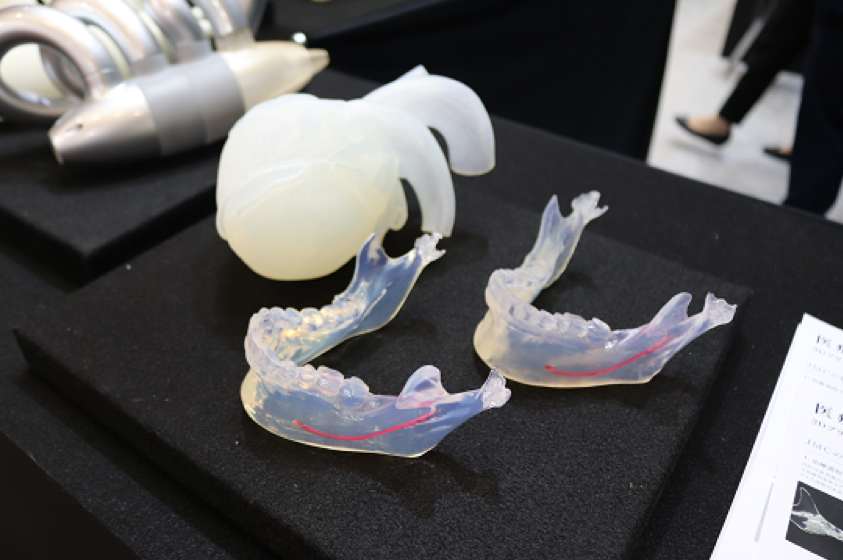
心臓モデル(左奥)と顎骨のモデル
1つ注目すべき分野として存在するのが、医療分野向けのソリューションです。工業と医療というと一見かけ離れた分野と感じがちですが、そうではありません。工業と医療は深く結びついています。内視鏡技術の発達などにも代表されるように、工業分野が医療分野の発展に寄与するケースも多いのです。特に3Dプリンター技術は医療分野との相性が良いという特長があります。人の身体という定量的な寸法では表現し得ない形状が3Dプリンターであれば造形可能だからです。
例えば医師が患者の心臓や頭蓋骨などの3Dデータを送ると、およそ1週間程度で患者のものと同じ心臓や頭蓋骨のモデルを製作するというサービスがあります。これにより医師はよりリアルな現物を見ながら手術などの治療方のシミュレーションを行うことができます。また以前に比べてエポキシやシリコン、ウレタンなど幅広い素材での造形も可能になりました。これにより、よりリアルな質感を持った医療モデルを再現することができるようになったのも大きな進化でしょう。シリコンなどの柔らかい素材を使って作られた心臓モデルとモーターを組み合わせることで心臓の脈動さえも表現できるようになります。これは特に内視鏡の送り込みのようなトレーニング分野での導入が期待されています。従来は医師の腕、つまりカンコツに頼ってきた部分に透明モデルを使うことで可視化。数値化することで作業を標準化していく試みなどが行われています。
3Dプリンター以外のソリューションの紹介
設計・製造ソリューション展には数多くの企業が出展しています。もちろん3Dプリンター以外の分野でも様々な企業が最新のソリューションを提案しています。ここでは、その中からいくつかをピックアップして紹介したいと思います。
関心の高いIoT系
会場を通して感じるのはIoTに対する関心の高さです。IoTとはInternet of Things、モノとインターネットが繋がる世界という意味です。2011年にはドイツで、インダストリー4.0として、国をあげてAIやIoTにより製造業に革新的な変化をもたらそうという動きが始まりました。それを受けて日本でもスマートファクトリーなどの呼び名で、製造業にIoTを導入する動きが広がっています。そのような情勢を反映するように、IoTに絡んだ出展をしている企業も少なからず存在していました。
設計・製造ソリューション展全体の傾向としては、やはり工程状況の確認などの分野にIoTを導入するというソリューション提案が多く見られました。工場や機械の稼働状況をタブレットなどオンラインで状況を確認するような内容が複数社にみられました。
シグナルタワーにセンサー取り付けた。イマオコーポレーション
イマオコーポレーションは治具メーカーです。実際にブースもソリューション展ではなく、機械要素技術展での出展でしたが、自社の治具の他に、自社の工場からスタートしたIoTによる生産管理ソリューションについても紹介していました。
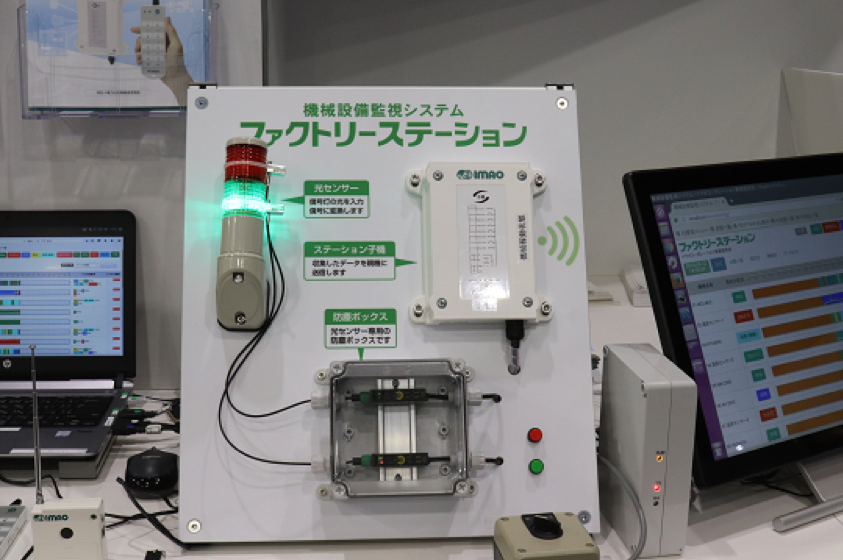
シグナルタワーに光センサーを取り付け機械の稼働状況を把握する
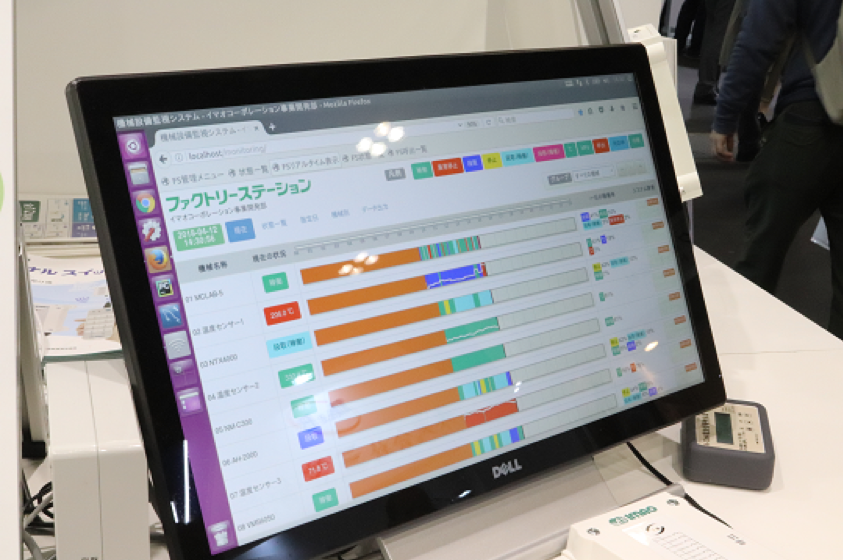
シグナルタワーから集められた情報は専用のWebサイトにて世界中どこからでも確認できる
継手メーカーもIoTに参戦。ジョプラックス社
ジョプラックス社は水道管やホースなどの継手を製作しているメーカーです。ジョプラックス社が提案するのは、浄水器に繋がる水のホースにBluetooth搭載の流量計を設置することです。
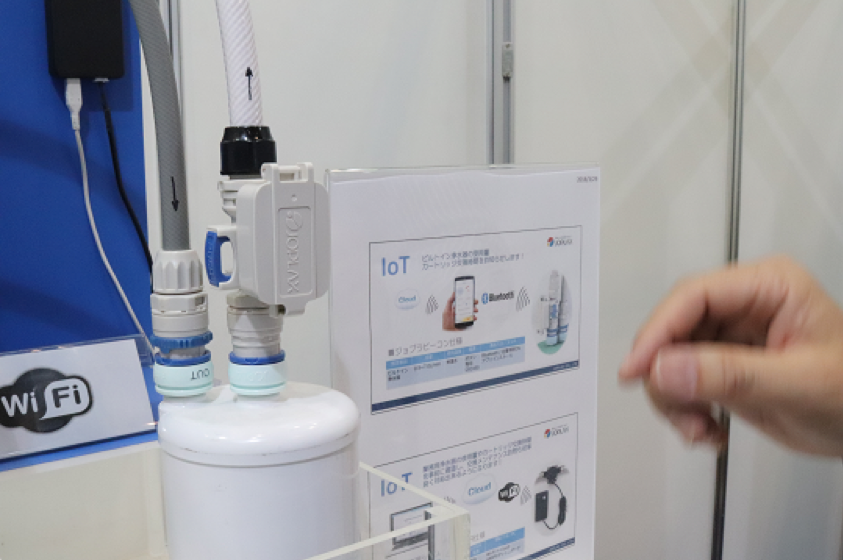
浄水器に取り付けられた流量計。これで浄水器の交換時期情報を収集する
計測された流量の情報はセンターに収集され、一括管理されます。これにより浄水器メーカーがフィルターの交換時期など一括で把握できるのです。ジョプラックスでは、コンビニのコーヒーマシンなど業務用、ビルトインタイプの浄水器を中心にIoTの導入をすすめています。今後は高齢単身者宅のトイレに取り付けて高齢者の安否確認を行う方法なども提案していきたいそうです。
記者のイチオシ
最後に全くの私見ですが、今回この名古屋ものづくりワールドを訪ねた中で個人的に興味を引かれた展示を紹介したいと思います。それはVERSTEC社が提案する新型旋盤です。
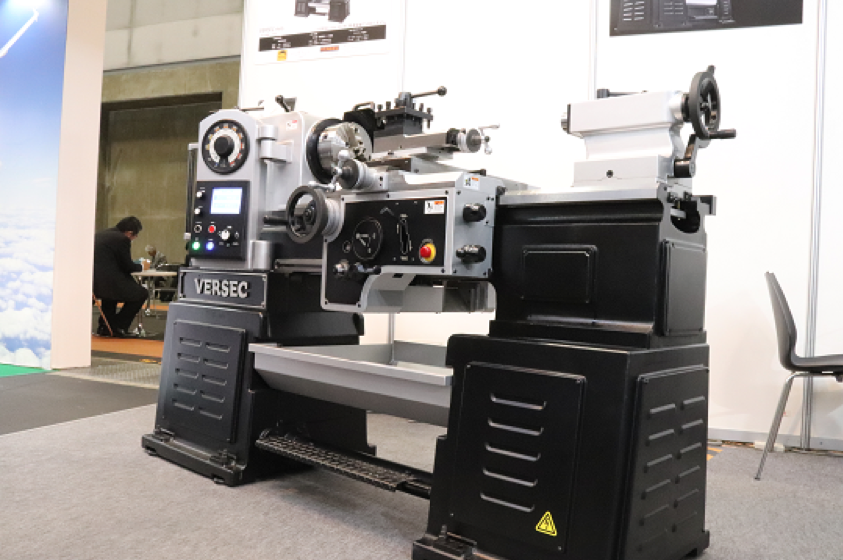
VERSTECが提案する新型の高機能旋盤
写真を見てもらえれば分かると思いますが、基本的な機能や構造は汎用旋盤そのものです。しかし従来の汎用旋盤とは異なり、チャックの回転数はギア比によって制御するのではありません。インバーターによりモーターの回転数そのものを制御します。これにより操作用のレバーの数などを減らし、若い層にも使いやすい機能を実現しました。さらにネジ切りのような簡単な定型加工についてはプログラムを内蔵。汎用旋盤でありながらまるでNCのように自動制御で加工を行うことができるのです。
金型製作や試作分野など、まだまだ汎用旋盤が活躍する場面も少なくありません。一方で昔ながらの職人の技術を継承できる人材の確保に悩む企業も数多くあります。このような高機能で使いやすい汎用旋盤の普及は技術力の維持に役に立つのではないかと感じました。
まとめ
国内外を含め、競争力を高めるためには、短納期、低コストでの試作、開発は避けて通ることのできない課題です。また、顧客の消費志向の変化により、顧客のニーズも多様化し、製造の現場にはこれまでとは違う多品種小ロット生産が要求されるようになりました。ここで紹介した 3Dプリンターの活用やIoTなども、やはり短納期・低コスト化、多品種小ロット生産という同じ課題へのソリューションです。激しさを増す競争の流れに取り残されないためにも、各社の提供するソリューションに関心を向けていくことが必要になるでしょう。
ライタープロフィール
工業の知識を持ち、現場を知るライターとして工業、製造業に関する取材や記事の執筆を行っている。 工学部機械工学科を卒業後、メーカーで設計エンジニアとして勤務。その後、趣味で書いていた文章をきっかけにライターとして独立した。
Why RICOH
(リコーだからできる事)
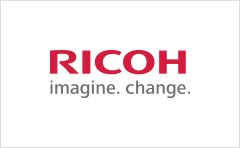
リコーは3Dプリンターをものづくりの現場で20年以上にわたって活用してきました。
製品の試作に始まり治具製造、さらには最終製品製造へと適用範囲を広げております。
2014年以降、自社で蓄積してきたノウハウを活かして
3Dプリンターの販売や3Dプリンター出力サービスを提供しております。
3Dプリンター出力サービスでは、お客様のご要望やご予算に合わせて
最適な造形材料・造形方式・後加工などをご提案しています。
従来の加工方法(切削/射出成型など)とは異なる、
3Dプリントの特性を最大限に活かした造形を丁寧にご支援します。