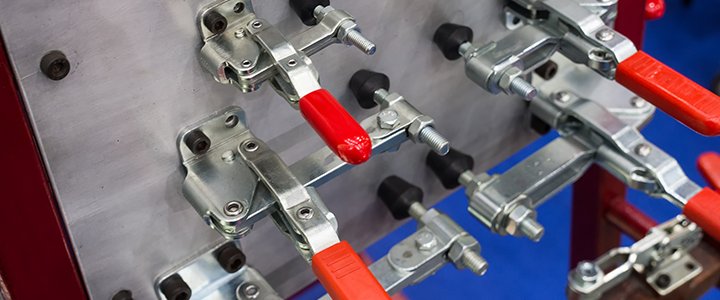
製品の加工、組み立て、検査に欠かす事の出来ない治具。治具製作には従来多くの時間とコストがかかっていました。これを解決するため、3Dプリンターによる治具製作に注目が集まっています。
加工、組み立て、検査に必要な治具
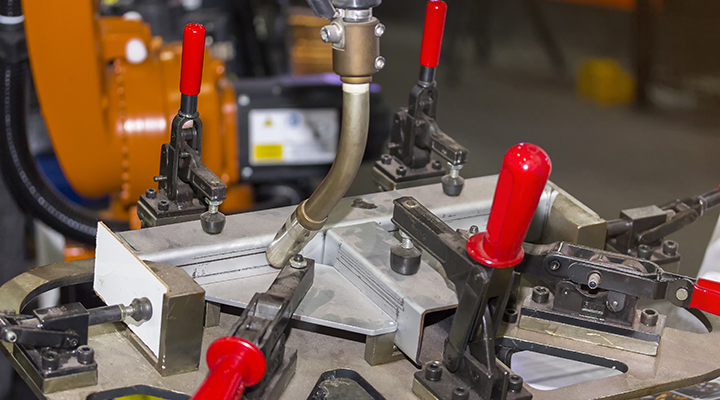
製品の加工、組み立て、検査を行う際には、様々な形状の治具を使用します。例えば、加工を行う際には、加工機に材料を固定する必要があります。この時、単純な円柱材や角材ならば簡単に加工機に固定できますが、段差や曲がりのあるような材料では、そのまま固定することができません。加工機と材料に合わせて作られた治具を介して材料を固定することで加工が可能となります。
加工位置に合わせた治具を使えば、加工前の位置合わせ作業が容易に行えるだけでなく、加工場所の誤りを防止できます。同様に、組み立てや検査においても、パーツ取り付け作業の容易化、取り付けミスの防止、検査装置の取り回し、検査装置の位置合わせなど、治具の用途は多岐に渡ります。治具が無ければ製品は出来ないと言っても過言ではありません。
このように、治具は製造の各工程で非常に重要な物であって、新しい商品を量産する際には、それに合わせた新しい治具が多数作られます。しかし、ここで問題があります。治具は何度も繰り返し使用されるため、キズや摩耗により精度が満たせなくなり、消耗品として何度も新しい物をつくる必要が出てきます。また、工程や取り付ける部品の変更、設計の修正があった際にも新たな治具を作る必要があり、新たな治具ができるまで数日から数週間製造が止まるという事もあります。他にも、本来ミスや手間を減らす為の治具なのに、種類が増えすぎて逆に工程を複雑にしてしまうという弊害もありました。
3Dプリンターを用いた治具製作により問題を解決
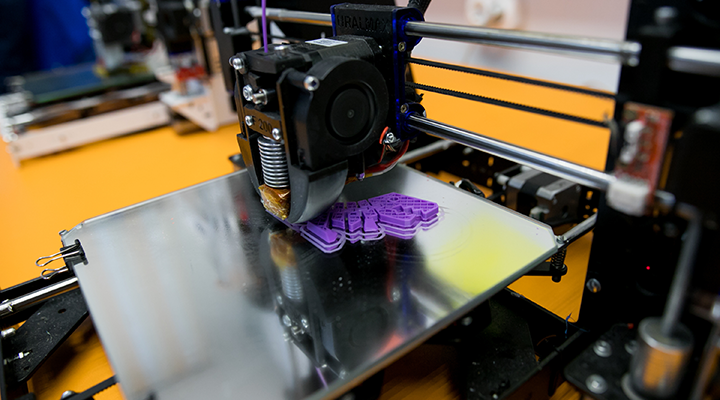
このような問題を解決する方法として、3Dプリンターによる治具製作に注目が集まっています。従来治具を外部に発注して製作するとなると、仕様検討から図面制作、仕様や図面の修正、加工などを合わせて早くとも2、3週間程度の時間がかかりました。しかし、3Dプリンターによる治具製作ならば、仕様検討から3D CADによるモデル製作、造形まで早ければ1日。長くとも数日で製作が可能となります。
製作時間が短くなるだけでなく、製作費も大幅に削減できます。それだけには留まらず、今までは作る事が難しかった複雑な形状の治具も容易に作る事が可能となります。これにより、部品や作業工程の変更に柔軟且つ素早く対応する事が可能となり、複数の治具を1つの治具にまとめて省スペース化することもできます。他にも、冶具の形状や造形に使用する材料を見直すことで治具の軽量化も図れます。治具の追加、修正にかかる時間やコスト、治具の種類の増加による工程の複雑化、重い治具による事故の危険性など、今まであった問題が全て解決されるのです。
ここで、3Dプリンターによる治具製作使用の一例として、小ロットの大型プリンターを製造するリコーインダストリー株式会社の事例をご紹介します。リコーインダストリーの国内工場では、組立工程で大量の類似部品を扱うため、部品の取り間違えなどのミスが発生しやすく、作業者の習熟にも多くの時間が必要でした。また、組み立てに必要な工具や治具がありましたが、種類が多く重い物も多かったため、作業者の負担となっていました。組立ミス低減と作業工程の改善、生産効率化が大きな課題でした。
/production/paragraph/images/image01s/d49/d49b7c52-e8e4-4c2b-9f93-44f80073acc9/original.jpg?jp.co.web-concierge-assets)
この課題を解決するため、3Dプリンターで造形した治具を積極的に活用する取り組みがはじまります。従来使用していた治具は、主に切削加工で作られた金属製の冶具だったので相当な重量がありました。作業者の安全と作業性の確保のため、治具は作業台に固定しなくてはなりません。これにより、生産工程の変更が難しく、作業スペースを奪う事にもつながっていました。これを3Dプリンターによるプラスチック素材の治具に変更することで、治具を大幅に軽量化することが可能となり、作業台への固定が不要となります。作業スペースを確保できるとともに、工程の変更へ柔軟に対応できるようになりました。
更に、3Dプリンターでは複雑な形状でも素早く低コストで製作できるので、部品に変更があっても、部品に合わせた形状の治具に素早く変更できます。例えば似た形状の部品が多い工程では、特定の部品しか置けない冶具を3Dプリンターで作ることで、新人作業者でも類似の部品を誤って取り付けることが無くなり、組み立てミスが大幅に削減されました。
また、部品の入ったトレーと同じ色に色分けした治具を作ることで、部品の取り出しミスを防ぐこともできるようになり、これによっても組み立てミスを大幅に削減しています。
このような3Dプリンターによる治具製作により、リコーインダストリー株式会社では、組み立て品質が向上し、月間不具合件数がゼロとなった上、生産ラインの大幅改革も実現し、生産効率が20%以上改善しています。今後3Dプリンターは、製造現場の現状を大きく変える鍵となります。
リコーインダストリーの3Dプリンター活用事例。3Dプリンターを活用した組立て治具製作と生産ラインの再構築により生産プロセス全体の見直しに成功。月間不具合件数はゼロになり、生産効率の向上を実現しました。
/production/paragraph/links/image01s/577/5774db31-2eeb-410f-a4df-dca895c67ddf/original.jpg?jp.co.web-concierge-assets)
ライタープロフィール
1972年生まれ。精密機械工学を専攻。東京都在住。製造業向け記事、テクノロジー全般を執筆。
Why RICOH
(リコーだからできる事)
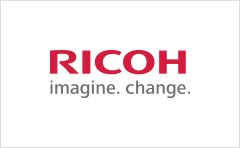
リコーは3Dプリンターをものづくりの現場で20年以上にわたって活用してきました。
製品の試作に始まり治具製造、さらには最終製品製造へと適用範囲を広げております。
2014年以降、自社で蓄積してきたノウハウを活かして
3Dプリンターの販売や3Dプリンター出力サービスを提供しております。
3Dプリンター出力サービスでは、お客様のご要望やご予算に合わせて
最適な造形材料・造形方式・後加工などをご提案しています。
従来の加工方法(切削/射出成型など)とは異なる、
3Dプリントの特性を最大限に活かした造形を丁寧にご支援します。