- #最終部品製造
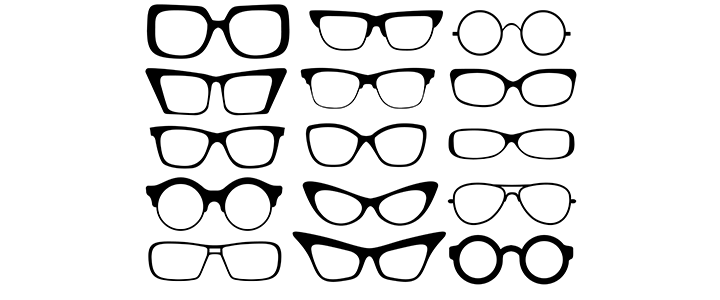
メガネの試作において3Dプリンターは既に活用されており、更には最終部品製造へのチャレンジも始まっています。「メガネは顔の一部です。」といわれるように、眼鏡はその形で大きく人の見た目を変えます。また、自分の顔の形にあった眼鏡を選ばないと耳や鼻に負担がかかり、痛みを生じることもあり、耳が痛くなり、ひいては頭痛や肩こりを引き起こすこともあります。「お客様一人一人が気にいるデザイン、顔の形状に合ったサイズを持つ理想の眼鏡の生産」。これを実現する為に眼鏡メーカーが3Dプリンターを活用して取り組んでいる活動をご紹介致します。
目次
市場に受け入れられるデザイン作りが鍵
眼鏡の市場には毎年毎シーズン、消費者のファッショントレンドを先取りしたデザインの眼鏡が多数登場します。視力矯正という機能も重要な一方で、眼鏡をかけた人の印象を大きく左右するファッションアイテムでもあるためです。大手眼鏡メーカーでは、マーケティングに力を入れ、さまざまな種類のデザインを企画し、試作を行い、製造を外部に委託するという形で消費者ニーズをとらえた製品を販売してきました。その過程では多数のデザイン案から市場に受け入れられるデザインを選び出さなくてはなりません。
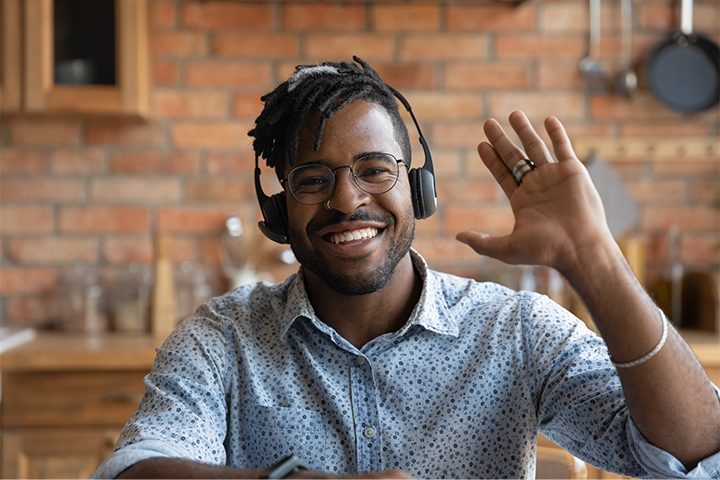
試作に3Dプリンターを活用してスピードを向上
試作分野ではすでに3Dプリンターは活用され、実際に手に取りながら上市する製品を検討することで、意思決定の精度を上げ、スピードを向上させる取り組みが行われてきました。その一つが3Dプリンターによる試作品製作です。簡易型や切削で試作を用意するとコストも納期も一定以上見積もる必要がありますが、3Dプリンターで眼鏡のフレームを造形するとその日のうちに仕上がります。短期間に試作品を繰返し製作しながら製品の完成度を上げることや、多数のデザイン案の実物をみながら比較し採用するデザインを決定することができます。こうした3Dプリンターを使った試作製作は、3Dプリンターの加工精度向上とともに、形状確認する際に費用対効果が高い手段として評価されてきました。
3Dプリンターによる最終部品製造する上での課題
最終製品製造段階では金型を使った生産を行います。金型を使用しての生産はコスト面や加工できる形状面での制約が存在しますが、高い信頼性をもった加工方法です。一方で3Dプリンターが造形できる材料は多くの場合限られます。社内の取り組み実績として眼鏡として利用できるほどの強度やねじれや衝撃に耐えた実績がなく、レンズをしっかりと支え、矯正視力に影響を及ぼさない高い精度での加工ができない懸念がありました。こうした「実績がないこと」が最終部品製造を3Dプリンターが担当する際の最大の課題でした。
3Dプリンターの可能性を信じ挑戦する企業が日本でも登場
福井県の眼鏡メーカーはHPのMulti Jet Fusion機を使ったサングラス製造に挑戦し、眼鏡全体の造形を行っています。クラウドファンディングを通じて事前に一定の注文数を確保し、その後発送するという受注生産を行っています。こうしたマーケティング上の工夫も行いながら、造形材料の色を活かした製品の仕上げをデザインする、ヒンジの部分で3Dプリンターでしかできない独自の形状に挑戦するなど3Dプリンターを活用したモノづくりに挑戦しています。
大手眼鏡メーカーでは、自社のハイエンドブランで最高のサングラスを作るという経営トップダウン型プロジェクトとして、3Dプリンターを活用したサングラスの販売を行っています。Carbon社の支援を受けながら、めがねのツルの部分で1㎜以下のラティス構造を活用した3Dプリンターならではの形状で製品をデザイン。一部店舗とネット販売で提供しています。
これらの取り組みは売れ筋製品の製造方法を3Dプリンターで代替しようというアプローチではありません。いままでにない特徴をもった製品を3Dプリンターという新しい工法を取り入れて開発した事例です。
いずれの取り組みでも、新しい製品開発を行う際に、試作を短期間に複数個作り、その試作を社内各部が連携し評価をおこない、そのフィードバックを受けて設計変更を行い一つ一つ課題を解決していきました。その結果、試作として煮詰めた完成度を、そのまま最終製品でも実現しています。
3Dプリンターにて最終部品を生産するメリット
金型を起こして量産を行う場合、一定のロット数を一度に生産して在庫を抱える必要があります。在庫の保管スペースにより倉庫や店頭、また財務上のバランスシートを圧迫しています。しかし3Dプリンターでの眼鏡の最終製品製造は、いままでのモノづくりの常識を覆す大きな可能性があります。移り変わる流行、また個々人の嗜好の違いに対応するために本来メガネは多品種少量生産が理想です。今後3Dプリンターでの製造を念頭に置いてデザインし、そのDataをもとに必要な時、必要な数、必要な場所で生産することで販売可能な資産に生まれ変わります。DX(デジタルトランスフォーメーション)にふさわしいデジタルなモノづくりの本領を発揮できるチャンスでもあるのです。
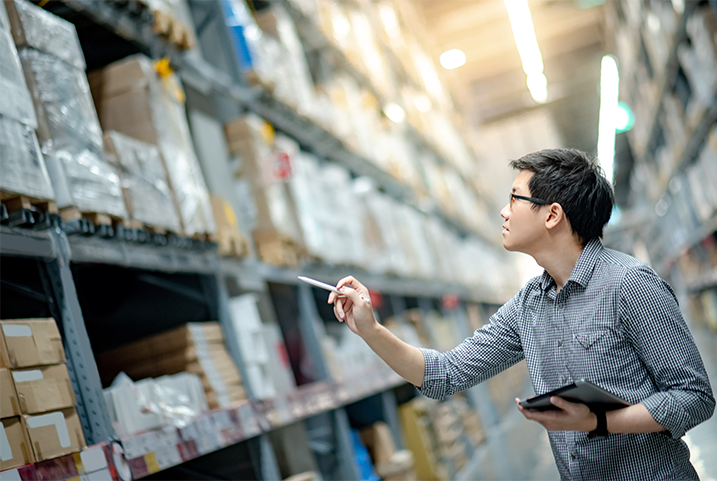
欧州では「一品一様」への取り組みも開始
欧州では眼鏡製造販売会社が3Dプリンター出力サービスと提携してお客様一人一人にジャストフィットする「一品一様」のメガネを提供している事例もあります。眼鏡店でお客様をスキャニングし、顔の形状、目と眼鏡の位置を正確に測定後、お客様が選んだデザインの眼鏡フレームを3Dデータ上で調整し、レンズの性能を最適化しながらも、かけ心地もぴったりとなる眼鏡の製造を行う取り組みを始めています。
眼鏡店に設置して眼鏡技師が手軽に利用者をスキャニングできる装置の開発から、基本フレームデータを顔の形状を基に最適化する処理や、さまざまなブランドが登録できる眼鏡デザインのライブラリの仕組みまで、サービスの生態系を構築するために必要なシステムを構築しています。
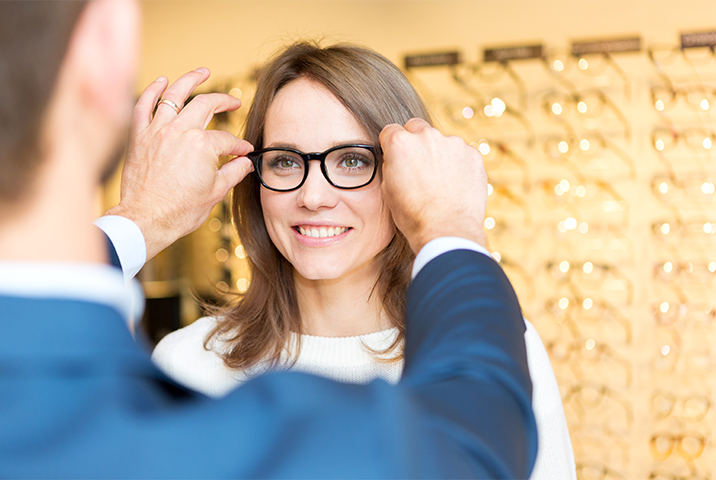
今後、日本でも「一品一様」のモノづくりに取り組む動きは出てくるでしょう。その際には、3Dプリンターでの造形だけでは成立しないことをこの例は示唆してくれます。利用者にあったボディフィットを実現するための計測、利用者の身体情報をもとに製品の形状を最適化するためのソフトウェア処理、そして最後に3Dプリンターをつかった一品一様の部品製造の3つのプロセスは必要になります。しかし3Dプリンターを活用することで新しいモノづくりがファッションやデザイン上の新規性だけでなく、利用者の抱える課題を解決できるとしたら、ビジネスモデル上の大きな競合優位性と成りえるでしょう。
Why RICOH
(リコーだからできる事)
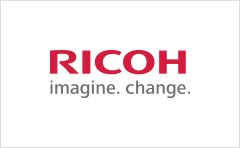
リコーは3Dプリンターをものづくりの現場で20年以上にわたって活用してきました。
製品の試作に始まり治具製造、さらには最終製品製造へと適用範囲を広げております。
2014年以降、自社で蓄積してきたノウハウを活かして
3Dプリンターの販売や3Dプリンター出力サービスを提供しております。
3Dプリンター出力サービスでは、お客様のご要望やご予算に合わせて
最適な造形材料・造形方式・後加工などをご提案しています。
従来の加工方法(切削/射出成型など)とは異なる、
3Dプリントの特性を最大限に活かした造形を丁寧にご支援します。