- #コラム
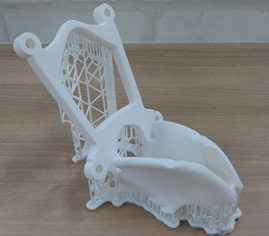
商品開発用の試作品製作を内製化するなど、3Dプリンターを活用している企業は年々増えていますが、活用のすそ野が広がったことで、「3Dプリンターならでは設計」への関心も高まりを見せています。弊社が実施した「3Dプリンター活用実態アンケート調査」では、3Dプリンターをお使いになって2年以上経過されている方では「3Dプリンターならではの設計」に対する関心が高いという結果が得られました。関心はあるけれどまだまだよくわからないという声が聞こえてきます。
そこで今回は「3Dプリンターならでは設計」に関してデータ・デザイン社の中で「3Dプリンターならでは設計」に取り組んでいる河根さんにお話を伺いながら、3Dプリンターで造形するときに、工法としての特徴をおさえた設計はどこから始めるべきか。ラティス構造やジェネレーティブデザイン、トポロジー構造といった本格的な3Dプリンターならではの設計に対する考え方などを伺いました。
(語り手:株式会社データ・デザイン 河根 伸泰氏、聞き手:3DPエキスパート編集部)
目次
「3Dプリンターならでは設計」に興味をお持ちの人が多いと思いますが、人にとっては領域が異なっている印象があります。河根さんにとっての「3Dプリンターならでは設計」を教えて下さい。
「3Dプリンターならでは設計」には、従来工法と比較して設計を変える領域、3Dプリンターの特徴を活かして造形物を最適化する領域の2つの領域があると思います。またそれぞれの領域も下記のように細分化されていると思います。
1 | 3Dプリンターの強みを活かした設計 | 従来工法と比較して設計を変える領域 |
2 | 4Dプリンターの弱点を活かした設計 | |
3 | インフィル・内部ラティス | |
4 | トポロジー最適化 | 3Dプリンターの特徴を活かして造形物を最適化する領域 |
5 | ジェネレーティブデザイン |
上記を順番に説明します。
1. 3Dプリンターの強みを活かした設計
3Dプリンターを使用する以前は、従来工法での製作を前提とした設計が行われてきました。例えば樹脂の射出成型、金属の鋳造はいずれも金型を使用して製作を行います。その場合、造形後、金型から取り出せる形状が必要になります。また切削加工では、切削できない形状、また非常に時間が掛かる形状を回避した設計をしてきました。またこれらの条件をクリアする為に一つの部品を複数に分解して製作し、造形後組み立てる方法をとっていました。しかし3Dプリンターでは型抜き等の縛りの無い設計、また複数部品を一体化することができ、大幅に製作時間を短縮することが可能です。
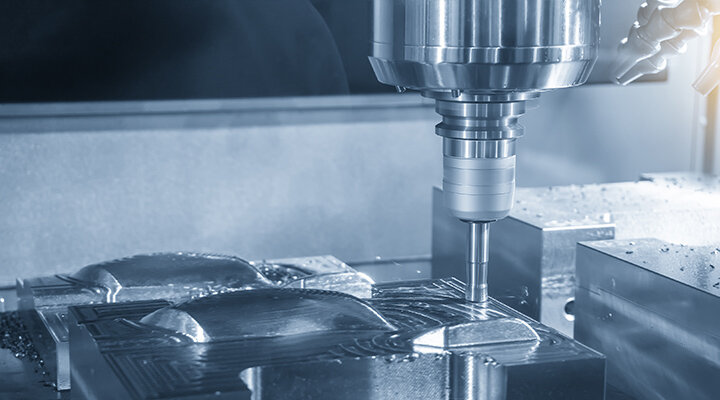
2. 3Dプリンターの弱点を補強した設計
一方、3Dプリンターは従来工法と比較して弱点もあります。機種にもよりますが極端に板厚が少ないものは造形できません。また形状によってはサポート材が必要で、そのサポート材を効率的に取り除ける形状が必要となる場合があります。
3Dプリンターを使い始めの方はこれらの障害にぶつかり3Dプリンターではなく従来工法で製作されている方も多数く見受けられますが、「3Dプリンターならでは設計」のすることで、これらの問題を乗り越えることが出来ます。下はその例です。
形状安定
3Dプリンターは形状が安定しないとお困りの場合は、形が崩れやすい箇所の形状変化を緩やかにする事で変形を低減できる場合があります。例えば楕円のアーチ状に形状を整える事で、厚みの変化を緩やかにすることで、積層時の変形を低減できます。
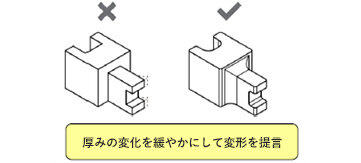
造形時間短縮
3Dプリンターは装置の性能向上が進んできたとはいえ、造形には一定の時間がかかります。複数のモデルを造形する際、造形時間を短縮するためには、パーツの容量を減らす事が有効です。肉抜きできる部分は積極的に抜いていく事を心がけると良いでしょう。

サポート材削減
3Dプリンターで同じように多く寄せられるご相談として、サポート除去が大変時間と手間がかかるという点です。円筒状の空間を設けてしまうと、形状が崩れやすくなるため、上部構造を支えるためにサポート材を多く使用してしまう場合があります。円の上部を構造的に強いティアドロップ型にすることで、サポート削減が可能になりますので、除去が用意になると思います。
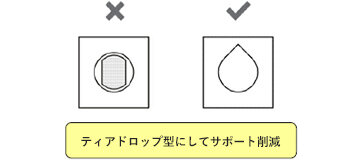
同じように形状がうまく維持できない場合があるのが、45度以上のオーバーハングがある場合です。45度以上のオーバーハングがある場合、サポート材が必要になってきますがサポート材を少なめにすると形が崩れる場合があります。該当箇所のオーバーハングを45度以下におさえることで、サポート材も抑制できますし、形状も安定するでしょう。
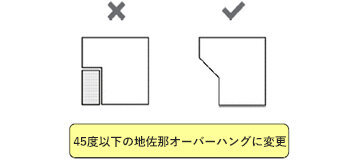
サポート材除去簡易化
同じように不要な角は面取りするようにしておくとサポート材を少なくすることが可能です。角を造形するために必要としていたサポート材を抑制すると、サポート材自体分割して造形できることも多いと思います。
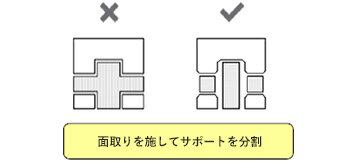
ここに上げた例は一部ですが、形状が安定しない、サポート除去が面倒、造形に時間がかかるといったご不満をお持ちの方には是非ご検討頂きたいポイントと言えるでしょう。実際に造形に利用する3Dプリンターの造形方式や機種によっての調整点があると思います。まずは取り組みやすいところから始めてみるのが大事かと思います。
ここまでの「3Dプリンターならでは設計」は、人が知識や過去の経験にもとづいたノウハウを活かして実施するものですが、ここからは、ソフトウェアを活用して「3Dプリンターならでは設計」を実現する方法を説明します。
3. インフィル・内部ラティス
MEX方式の3Dプリンターをお使いの方はご存じだと思いますが、造形する際に、3Dプリンターの造形制御ソフトに、内部の密度を下げて造形速度を速くする設定項目があります。これをインフィルレート調整といいます。 Markforgedの造形制御ソフトEiger(アイガー)では一般的なお客様の使用実績を反映し初期設定値を37%に設定しています。
造形物の使用目的にもよりますが、デザイン性確認等が主目的の場合、インフィルレートを下げて造形しても問題がない場合が多いようです。これが3Dプリンターの特徴を活かしたソフトによる修正の第一歩だと思います。(下図は造形物の内部断面)
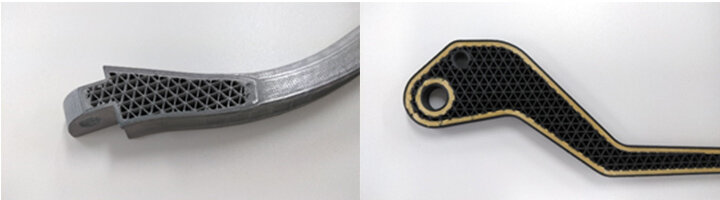
インフィルレートは単純に中空率を変化させるので、中空率を上げると強度は低下します。しかし造形物の内部をラティス構造にて中空にすると強度的に有利です。NETFABBのラティス最適化機能では応力を考慮した最適なラティス構造を造形物の内部に作ることができます。これはもう一歩進んだソフトによる3Dプリンターの特徴を活かした最適化といえると思います。
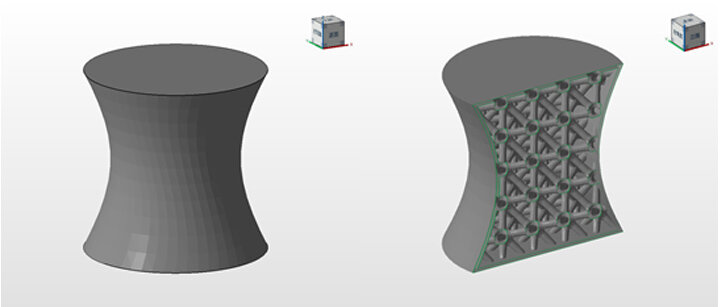
4. トポロジー最適化
3Dプリンターならではの設計手法で、ラティスと並んで取り上げられるのが、トポロジー最適化です。トポロジー最適化とは、対象の部品に求められるサイズ・強度等の条件をもとに、最適な材料の密度分布を導き出す、構造最適化手法の一種といわれています。当初の機能を持ったまま、部品の軽量化を実現し、3Dプリンターでは造形時間の短縮や、使用材用の削減を達成することができます。こうした最適化は設計者が一つ一つ設計するのではなく、設計要件を投入することで、現在トポロジー最適化を実現できるソフトウェア(FUSION 360の形状最適化機能等)を利用して取り組むことができます。(画像AUTODESK)
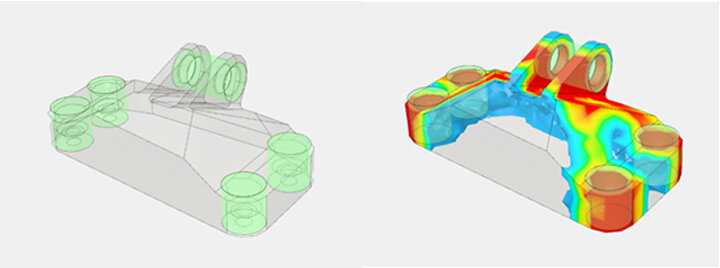
シミュレーションの後、応力の影響がない部分を削除するなど強度を保ちつつ軽量化を行う
5.ジェネレーティブデザイン
先ほどご紹介したトポロジー最適化と同じ設計最適化手法として、ジェネレーティブデザインと呼ばれる設計手法もあります。コンピューターが自動で複数のデザインを起こしてくれる技術という意味では同一なのですが、処理を行う際に、対象となる部品にかかる荷重の組み合わせを基に、製造方式を想定した形状を算出してくれます。
弊社では実際に、レーザープロジェクターを三脚に固定するためのマウントを製作してみました。ジェネレーティブデザインにしろ、ラティス構造にしろ、設計者が自分でモデリングするのではなく、指定したパラメーターをもとに、専用ソフトウェアが半自動でモデリングするというアプローチになります。
レーザープロジェクターの場合ですと、レーザープロジェクター本体を支えるための点と、三脚とつなぐための点は必ず必要となります。こうした絶対に必要な部分を指定する必要があります。またマウントとレーザープロジェクターの本体と干渉しないように、本体部分にマウントがかからないように指定する必要があります。その後、その点に対してどのような力が加わるかを指定していきます。この場合は、レーザープロジェクターの重量や、セットする際にかかる荷重をニュートンで指定していく形です。その際にどの程度軽量化するかなど、ジェネレーティブデザインでどれくらい安全をみるかなどを設定していくことができます。材質も指定できるので、あとはソフトウェア側で要件にあったデザインモデルを複数パターン、自動で設計してくれます。
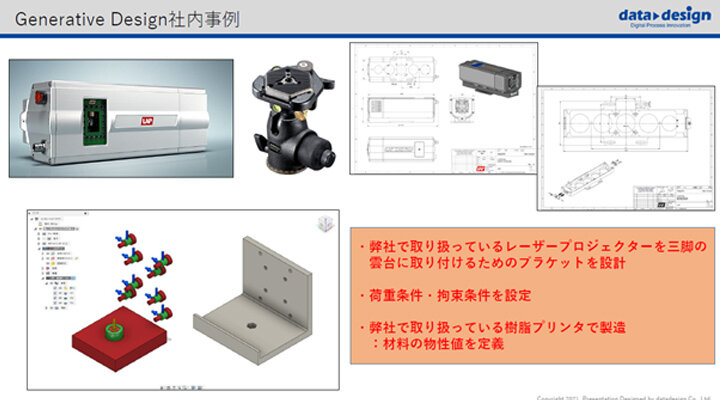
設計バリエーションが自動で何種類も出てくるわけですね。
はい。製造する工法も指定できるので、切削でつくることを念頭においたデザイン案も可能です。設計者として見ると、自分が設計するときは、イメージしなかったような奇抜な設計になって出てきます。よい意味で期待を裏切られることもあれば、違和感を持つ場合もあるでしょう。私は自分にない引き出しをみせてもらったような驚きと、構造的にはすこし頼りない印象をもちました。実際に3Dプリンターで造形して、マウントとして利用してみると、若干強度的にふわふわした印象をもちましたので、レーザープロジェクターをもっと安定して保持できるように、構造を太めにするように、自分で手をいれて、調整しました。

ある意味、ソフトウェアのチャレンジングな設計案を、他の部品との兼ね合いや利用者のことを意識した設計者がバランスさせていくような、コラボレーションがあったわけですね。
そうかもしれません。今回ご覧いただいた当初案では、実際には持ち運びや保管、落とした際でもある程度大丈夫なように、といった仕上がり部品の利用環境を網羅したパラメーター設定ではなかったので、上がってきたデザインをみながら設計者が修正していった形でしたが、設計者が思いもつかない形状を提案されることは、設計者にとって、よい刺激になるかもしれません。
まとめ
Why RICOH
(リコーだからできる事)
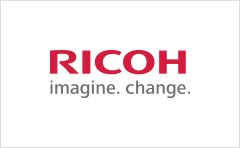
リコーは3Dプリンターをものづくりの現場で20年以上にわたって活用してきました。
製品の試作に始まり治具製造、さらには最終製品製造へと適用範囲を広げております。
2014年以降、自社で蓄積してきたノウハウを活かして
3Dプリンターの販売や3Dプリンター出力サービスを提供しております。
3Dプリンター出力サービスでは、お客様のご要望やご予算に合わせて
最適な造形材料・造形方式・後加工などをご提案しています。
従来の加工方法(切削/射出成型など)とは異なる、
3Dプリントの特性を最大限に活かした造形を丁寧にご支援します。