- #コラム#試作製造#透明材料
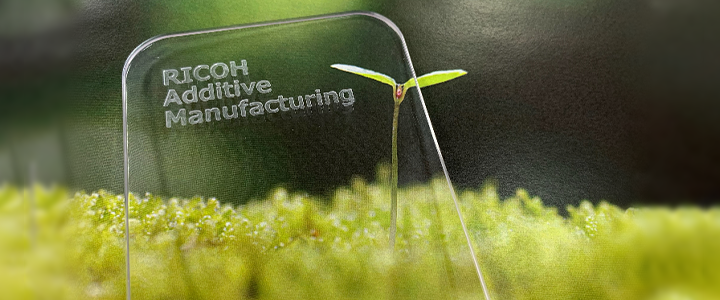
リコージャパンでは毎年3Dプリンターに関心がある企業を対象とした利用実態調査を実施しています。その調査によると、自社で3Dプリンターを保有しているにも関わらず、社外の3Dプリンター出力サービスを利用されていると回答した企業が一定数いらっしゃいました。材料の観点で大きな理由として挙げられていたのは「透明材料」を利用したいという回答でした。3Dプリンターを所有されているお客様がわざわざ社外に発注する「透明材料」の用途どのようなものなのでしょうか?
リコーグループには複写機の開発・設計を実施している部門がありますが、自部門で3Dプリンターを保有しているにも関わらず、リコージャパンの3Dプリンター出力サービスに「透明材料」で造形依頼をしています。今回はその部門にいる設計者たちに、所有している機器の活用状況、また、「透明材料」の用途等を詳しく説明して頂きました。今後の3Dプリンター及び透明材料活用のヒントになれば幸いです。
(取材協力:リコー株式会社 RDP WE事業部 有田大介、養田泰信、小島玲央)
目次
自部門の3Dプリンターで30%、出力サービスでの20%の試作品を製作
現在どのように3Dプリンターを業務でお使いですか?
私たちは複写・印刷ができる複合機の開発・設計・生産準備をプロジェクトチームで担当しています。各モジュールをチームに分かれて開発、それぞれのモジュールを集めた製品設計、生産準備を行うのですが、各プロセスで、形状を確認するための「簡易試作」、機能を確認する「機能試作」の為の試作品を製作する必要があります。その試作品は自部門の3Dプリンターで約30%、出力サービスで約20%、残りは従来工法の切削、貼り合わせなどで製作しています。
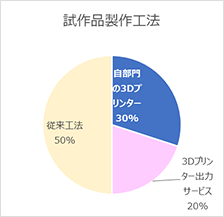
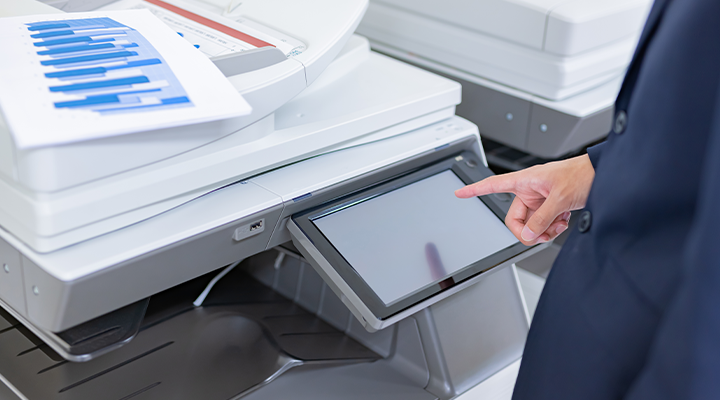
3Dプリンター活用の最大のメリットは納期短縮
3Dプリンター活用のメリットを教えて下さい。
3DCADにて設計後、社外に切削・貼合わせを依頼する場合は通常は2Dの図面で依頼をするのですが、2D図面作成に2日ぐらいの時間が掛かります。また自部門以外で作成すると費用が発生するので、社内で発注承認、また検収・支払い処理等の事務処理も必要となります。下図でも示していますが、自部門の3Dプリンターや3Dプリンター出力サービスを利用した場合、社外の切削・貼合わせと比較して大幅に納期を短縮できることは大きな魅力を感じています。
単位:日
3DCADから 2D図面作成 |
社内発注承認 | 製作 | 検収・支払 処理 |
合計 | |
切削・貼合わせ | 2 | 2 | 15 | 1 | 20 |
3Dプリンター 出力サービス |
0 | 2 | 5 | 1 | 8 |
自部門 3Dプリンター |
0 | 0 | 1 | 0 | 1 |
また費用も小さな樹脂の部品を貼り合わせで依頼すると最低でも3万円、少し大きな部品だと10万円を超えてきます。自部門の3Dプリンターの場合コストも材料費のみで済ませることができ製品開発費用の削減につなげることができます。
自部門の3Dプリンターを使うから複数形状の試作品を製作できる
製品設計をしているときに自分でも2-3の案が出来てきてCAD上ではそのどれにするか決定できないことがあります。特に自部門に設置された3Dプリンターで造形する場合は納期とコストのメリットがあるので、CAD上で2-3の案を作成しそのまま3Dプリンターで製作し製品に組付けてどの案が良いか、また別の案があるかを短い時間で確認ができるようになったことも非常に助けられました。
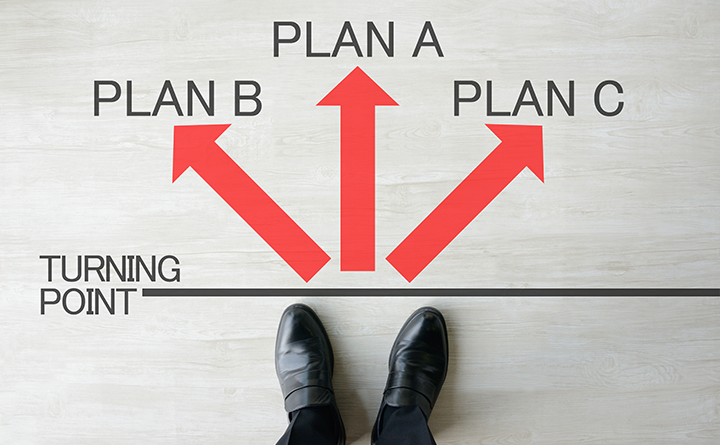
透明材料で外装カバーを製作し、機内の配線の這いまわしを確認できる
透明材料はどのように活用されていますか?
製品の操作を行う「操作部」は担当の機種では下記のようなタブレット状の形状をしています。
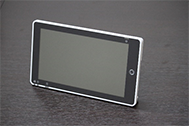
その操作部の背面カバーの試作品を『リコー3Dプリンター出力サービス』に依頼して透明材料にて製作してもらっています。
操作部は厚みの低減、軽量化を目指し可能な限りコンパクトにすることを狙って設計しているので、機内の配線用の配線を這いまわすスペースも最小限にとどめたいと考えています。私たちの部門では、VRゴーグルでバーチャルに製品組立後の機内での部品の位置を確認する取り組みも行っているのですが、配線周りなどを組み込んだ際には、配線のコシがでると他部品に接触、無理に折り曲げて組付けられると品質問題が発生するリスクがあります。そのため、『リコー3Dプリンター出力サービス』で対応している高透明材料で外装カバーを用意することで、組立後、機内の配線を目で見て確認できるので、必要に応じてクランプの追加、バインドを使用して配線を束ねる等問題解決方法を早期に見つけることができます。
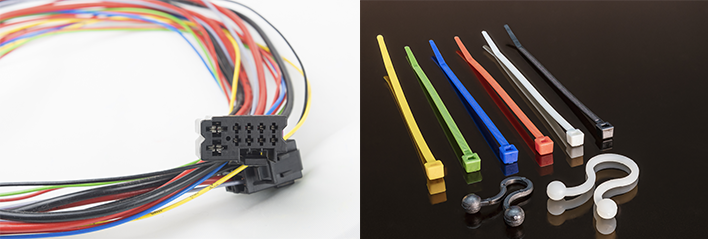
透明材料で外装カバーを製作し、機内の用紙先端の動きが確認できる
その他透明材料はどのように活用されていますか?
複写機のスキャナー部分に自動で原稿紙を送るモジュール部分ですが、原稿は通常の用紙より種類が多く、厚み、表面性、コシが異なる様々な原稿をスピーディーに確実に送る必要があります。また、お客様の大切な原稿なので紙詰まり等発生を極力抑えることが重要です。しかし、その原稿自体の吸湿度合い、また使用する部屋の温度、湿度等、また、ゴム部品の経年劣化等の条件によっても結果は異なります。
リコーには複写機開発・生産の長い歴史があり、試作の段階でどのような動作をしていると、どのような結果が出るか予想が付きます。したがって原稿送り装置はモジュール開発の段階で、原稿がどのように機械内部で動いているか、狙った通りの「たわみ」がでているか?「傾き」はどの部分で発生しているか試作品を組み立てて動作を確認しています。今までは原稿送り装置の外装カバーに穴を開け、小型CCDカメラを差し込んで機内を観察していましたが、全体を俯瞰することは困難でした。
そこで下記のようにリコー3Dプリンター出力サービスで対応している高透明材料にて試作品を製作してもらいました。この試作品を組付けて稼働させることにより、狙い通りの原稿の動きができているか自分の目で確認することにより、問題が発生した場合もその原因を早期に発見出来るので大きく製品開発のスピードアップにつながったと感じています。
3Dプリンターを使用し始めて5年、今、思うこと...
最初に自部門に設置された3Dプリンターを使い始めてから約5年経過しています。当初は3DCADで設計したファイルでそのまま造形できること、納期・コストのメリットに驚かされました。しかし表面の精度や強度の面の問題もあり3Dプリンターで製作する部品は一部に限られていました。その後口コミも含めて社内で使用する人数が徐々に増加していき、材料変更、造形の方向等目的に合った造形のやり方を見つけ出し情報交換をすることによりスキルとして社内に蓄積され出しました。また3Dプリンターで製作した後に追加工、後処理を加えて当初の狙い通りの試作品が製作することができるとわかり、益々3Dプリンターの使用率が高まってきました。
2年前からリコーグループ内の3Dプリンター出力サービスに依頼し始めて、自部門の3Dプリンターでは造形できないサイズ、使用できない材料を使って製作することが出来るようになりました。また3Dプリンター出力サービス部門には長年メカ設計の経験を積んだ技術者がいて、造形の依頼をすると、最適な3Dプリンターの方式、材料、造形する方向、また元図面に対しても助言をしてくれます。
これらの活動により現在は樹脂部品の現在は約50%の試作を3Dプリンターで製作することが出来るようになりました。数年がかりになることも珍しくない複写機の開発プロジェクトですが、新しい技術要素の取り込みや機能改善を続ける中で毎回苦労があります。予定通りに物事がすべて進むことはまれで、予期しない障害への対応や、関連部署とのすり合わせで設計変更を行うこともまれではありません。プロジェクトも終盤になってくると時間との戦いです。問題発生時に対策がすぐに見つかれば良いのですが、試行錯誤してベストな方法を見極めなければならないこともあります。その場合一つの試作品を用意するために20日掛かっていると、全体の製品開発日程に大きく影響を与えてしまうこともあります。迅速に仮説検証を繰り返し行うことができる3Dプリンターによる試作の調達はプロジェクトの安定性を大きく向上させてくれると感じています。
小島玲央、有田大介
まとめ
実際にモノづくりの現場で設計開発に取り組んでいる現場の中から、3Dプリンターを使用している設計者の視点からご紹介してみました。3Dプリンター活用のメリットは「低コスト」・「短納期」・「現物があることですり合わせが容易」という3点があげられました。またデメリットは「強度」や「機能要件を十分満たせない場合がある」という点に集約されました。また透明材料に関しては、見ることができない内部構造などを目視できることで、「開発時の課題解決に貢献できる」点が大きなメリットであることがわかりました。
3Dプリンターは万能な道具ではありません。得意なこと、苦手なことを理解した上で、試作開発を高速化させるために3Dプリンターの特徴を踏まえて活用していく姿勢が重要になってきます。また3Dプリンターは装置性能や取り扱いできる材料の多様化が進むスピードが速い日進月歩の分野です。スーパーエンプラで耐熱性が高い部品を造形可能であることをこの取材のあとで紹介すると日常的に装置に触れている今回の設計者も驚いていました。技術進歩に関しては3DPエキスパートのメールマガジンなどでもお伝えしていきますが、3Dプリンター界隈の進歩に関して、常にアンテナを張って業務への活かし方を考えていくことも重要になってくるといえそうです。
Why RICOH
(リコーだからできる事)
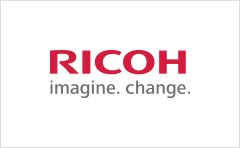
リコーは3Dプリンターをものづくりの現場で20年以上にわたって活用してきました。
製品の試作に始まり治具製造、さらには最終製品製造へと適用範囲を広げております。
2014年以降、自社で蓄積してきたノウハウを活かして
3Dプリンターの販売や3Dプリンター出力サービスを提供しております。
3Dプリンター出力サービスでは、お客様のご要望やご予算に合わせて
最適な造形材料・造形方式・後加工などをご提案しています。
従来の加工方法(切削/射出成型など)とは異なる、
3Dプリントの特性を最大限に活かした造形を丁寧にご支援します。