- #コスト低減 #納期短縮
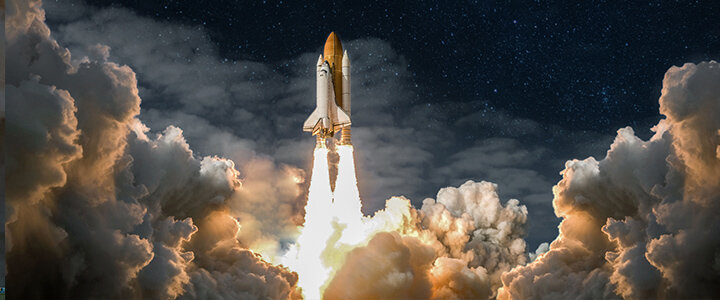
プロファイル
企業 | 航空宇宙関連メーカー |
---|---|
部門 | 工場生産企画・管理部門 |
活用状況 | 設計・開発・製造で3Dプリンターの利用実績はありましたが、治具への本格的な活用検討を開始。 |
事例概要
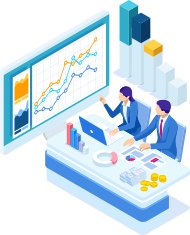
- 航空宇宙分野での最終部品製造にも3Dプリンターを活用されていたものの、治具分野への展開はあまり進んでなかったとのことでした。
- 部品の設計変更のたびに、金属製治具の変更を外部に委託していたが、3Dプリンターにて樹脂にて内製化することにより、調達コストと調達期間の大幅改善を実現。
- また、従来の金属製治具はメンテナンスに多くの工数を取られていましたが、樹脂化された治具は低コストなので定期的に交換することにより省力化に成功。
航空宇宙部品向けの治具製作の課題
設計変更頻度が多く治具をそのたびに再調達
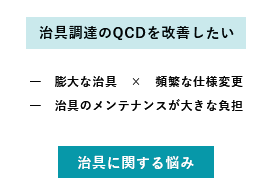
高い信頼性が求められ、性能向上のための設計変更も頻繁な航空宇宙業界向け部品を製造していくために、製造ラインでは数多くの治具が活用されていました。その数は万単位の数におよぶ上に、設計変更のたびに、治具の仕様もかわる為、治具調達におけるQCD改善は、製造現場での大きな課題になっていました。
金属製の治具はメンテナンスにも手間がかかる
また金属製の治具は定期的なメンテナンスが必要です。複雑な形状の治具をメンテナンスする為に、適切なスキルのある人員がすくなくない時間拘束されてしまいます。見えないコストとしての治具メンテナンスも大きな課題となっていました。
効果的に3Dプリンター活用するためのステップ
まずは3Dプリンターで調達できる治具の洗い出しから
設計・開発現場にも3Dプリンターが導入されており、最終部品にも金属3Dプリンターでの造形を取り入れていた事もあり、早い段階から製造現場内の治具に関しても3Dプリンターを導入していきたいという声があったため、まずは対象治具の洗い出しと導入効果を可視化していく事からはじめました。
製造現場内の治具を工程別にリストアップし、材質やサイズ、求められる強度、形状の複雑さ、想定される調達頻度、コストなどを元に評価。社内で3Dプリンターを導入して製造するもの、外部のサービスビューロに製作を委託するもの、従来通りの調達経路で調達するものに分類し、改善効果が高いものから実施する計画を立てました。
評価造形後に1台導入して概念実証
評価造形を通じて製造現場内で治具製造のために利用する3Dプリンターを選定。1台導入し、造形を行いながら概念実証を推進。納期的にもコスト的にも特に大きな成果を収めたのは、アルミ材の治具をスーパーエンプラ材に材料置換して造形した取り組みです。
造形時には社内で治具の再設計を行い、部品統合や軽量化を行い製造性を高めるなどの取り組みをおこなうことで、デリバリーは3分の1に短縮し、製造コストも50%以上の削減を実現できたという事です。
耐薬性が求められる塗装治具にも
スーパーエンプラ製の治具は塗装ラインで用いられる塗装治具にも適応できました。耐熱、耐薬性のある造形材料を用いる事で、交換頻度の高かった塗装治具の調達コストの節減に大きな貢献を果たしました。
その都度造形することで金属製治具のメンテナンス工数を大幅節減
また調達以外にもメンテナンスの面でも材料置換は大きな貢献を果たします。金属よりも安価で、3Dプリンターで製造できるスーパーエンプラ製の治具であれば、定期的な点検の結果、問題があれば再製作が容易です。定期的なメンテナンスを行う工数を加味すると再製作して製造ラインへの影響を最小限に抑える事は充分コスト的に見合うという結果も導き出せた為、工数の削減にもつながりました。
複数台導入で効果を一層拡大
狙い通り、多くの工程での治具を樹脂3Dプリンターで造形することで、調達コストの節減、リードタイムの短縮が実現できました。製造現場に追加で3Dプリンターを複数台導入し、治具内製化の範囲を拡大し、恒常化させることで製造コストの合理化を継続して実現します。
3Dプリンター製治具へのリプレイスを拡大
今回の治具調達の大きな見直しの結果、以下のような結果を得ることができました。
新規治具の導入時のQCDを改善できた為、今後はメンテナンス負荷がかかる治具のリプレイスを拡大していきます。
- 解決した製品/サービスはこちら
-
-
マテリアルジェッティング方式(MJ方式)の樹脂3Dプリンター。3種類の素材を同時噴射することで、複数材料からなるパーツやアセンブリを単一工程で造形することができる。複数樹脂を組み合わせたデジタルマテリアルによってより最終製品に近い質感をもった造形物の出力が可能。
-
豊富な保有設備と社内外の造形依頼に対応してきた経験を活かした造形サービスをおこなうリコーの3Dプリンター出力サービス。
造形サービス以外にも、プリプロセス(紙図面からの3DCADデータ起こし、ワークを3Dスキャニングし3Dデータ化するリバースエンジニアリングなど)や研磨などの後加工もワンストップで提供。
-
Why RICOH
(リコーだからできる事)
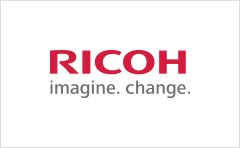
リコーは3Dプリンターをものづくりの現場で20年以上にわたって活用してきました。
製品の試作に始まり治具製造、さらには最終製品製造へと適用範囲を広げております。
2014年以降、自社で蓄積してきたノウハウを活かして
3Dプリンターの販売や3Dプリンター出力サービスを提供しております。
3Dプリンター出力サービスでは、お客様のご要望やご予算に合わせて
最適な造形材料・造形方式・後加工などをご提案しています。
従来の加工方法(切削/射出成型など)とは異なる、
3Dプリントの特性を最大限に活かした造形を丁寧にご支援します。