- #コスト低減 #納期短縮
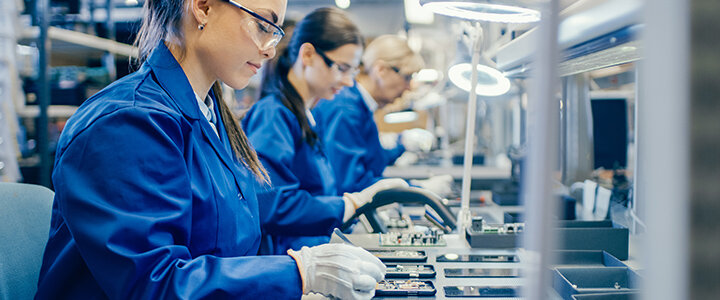
プロファイル
企業 | 海外 部品製造会社 |
---|---|
部門 | 複数種類の部品を製造する工場生産企画・管理部門 |
活用状況 | 本社開発部門では3Dプリンターを活用していたが、製造部門としては活用実績は無し。 |
事例概要
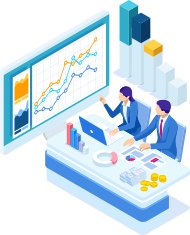
- 製造現場の組み立て工程を観察し、各工程にかかる所要時間やミスをパターン化し細かい改善に取り組んでいる中で、作業者によってばらつきがある工程をピックアップ。
- 作業を標準化するための組立治具を現場が企画、設計し製造現場にある3Dプリンターで造形することで、細かい改善を標準化した上で実現していく事に成功。
従来はどんな課題があったのですか︖
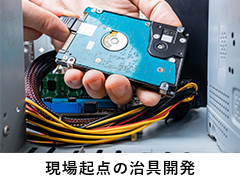
改善の為に作業をカメラで撮影し分析
単純な工程でも作業者によって作業時間にばらつきがでたり、品質が安定しない工程が存在することがあります。
製造現場内でカメラによる自動撮影を導入し、各工程でかかる時間や作業を記録し分析して改善案を作成しました。
改善の為の治具を外作すると手間とコストが掛かる
改善の為に現場起点での治具活用が重要になりますが、治具を従来通りの方法で外注先に委託していたので、準備期間や調達コストが肥大化し、改善案までに長い時間が必要となってしまいました。
一例をあげると、熟練工は電子基板にコネクターを差し込む際にスムーズに作業できますが、非熟練工は基板にコネクターをうまく挿入できず時間をロスしてしまったり、コネクターのピンを折ってしまうケースが発生していました。
こうしたASSYプロセスをミクロに見ていく事で改善機会は無数にミエルカできるのですが、課題の見える化にとどまらず、タイムリーに、製造現場の作業員が作業内容を改善するための指導、改善方法を提供していく必要がありました。いかに早く多様な治具を現場に投入し、QCDを改善していくか。その実現が製造現場のモチベーションにもつながってくるとあって、重要な課題となっていました。
3Dプリンターでどのように課題を解決されましたか︖
治具を3Dプリンターで造形
先ほど取り上げたPCB基板にコネクタを挿入する工程では、正しい位置から正しい角度で挿入することが重要なポイントでした。そのために、PCB基板にフィットし、コネクターの挿入位置をわかりやすく明示できる組立治具を設計し、3Dプリンターで製造しました。治具を2つのパーツにわけ、コネクターをPCB基板に挿入する際の動きをガイドするようにスライドできるように造形することで、作業員によってばらつきがあったコネクターの挿入位置と角度を標準化。非熟練工でもミスなく短時間で組み立てができるよう改善できたとのことです。
改善ポイントを洗い出し、作業方法の見直しや治具の導入などで作業者の支援を具現化すること。また一過性の取り組みに終わらず継続して積み重ねていくことは、現場起点の改善の重要なプロセスです。
社内3Dプリンターと提携サービスビューローを活用
今回のケースでは、期待できる効果と取り組みやすさによって優先順位付けを実施。その中で、製造現場内にある3Dプリンターで治具を開発し対応するもの、提携サービスビューロや治具製造会社に協力を依頼するものにわけて改善を具現化するための実施計画を整備。
短いサイクルで何度もPDCAを回すことによりQDCの改善を実現
製造現場内で取り組みを行う施策では、改善案を企画したチームと密接にやり取りを行い、ポンチ絵、設計図、試作など各段階ごとに意見交換を実施。実際に治具の試作ができてからは複数人で実際に工程の中で利用してみるなど、企画と検証を短いサイクルの中でPDCAを何度も回し、効果を定量的に計測していきました。その結果、複数の工程で小規模な治具開発と導入を行うことで、製造ラインのQCDの改善を実現。
3Dプリンター導⼊後の効果はいかがですか︖
今まで現場から改善に対する意見が上がっても、治具作成等ののコストが障害になり精神論で止まり着手できなかったケースが多くあったが、3Dプリンターの活用により改善を具現化できることが大きな自信につながりました。
- 解決した製品/サービスはこちら
-
-
Raise3Dは、低価格でありながら高精度と多種多様なフィラメントに対応している3Dプリンター。比較的安価な3Dプリンターでは珍しい可動式デュアルヘッドを搭載することで、単色造形だけでなく二色造形、サポート専用材を使用した造形を安定して行えます。
-
Formlabs社独自の「Low Force Stereolithography(LFS)™」技術は、光造形(SLA)方式への全く新しいアプローチで、レーザーとミラーを包含したLight Processing Unit(LPU)を使用し、造形の微細さと速度を両立しながら液体樹脂を等方性を持つパーツに硬化させます。
-
Why RICOH
(リコーだからできる事)
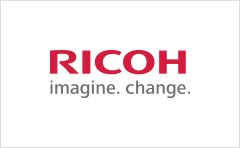
リコーは3Dプリンターをものづくりの現場で20年以上にわたって活用してきました。
製品の試作に始まり治具製造、さらには最終製品製造へと適用範囲を広げております。
2014年以降、自社で蓄積してきたノウハウを活かして
3Dプリンターの販売や3Dプリンター出力サービスを提供しております。
3Dプリンター出力サービスでは、お客様のご要望やご予算に合わせて
最適な造形材料・造形方式・後加工などをご提案しています。
従来の加工方法(切削/射出成型など)とは異なる、
3Dプリントの特性を最大限に活かした造形を丁寧にご支援します。