- #コスト低減 #納期短縮
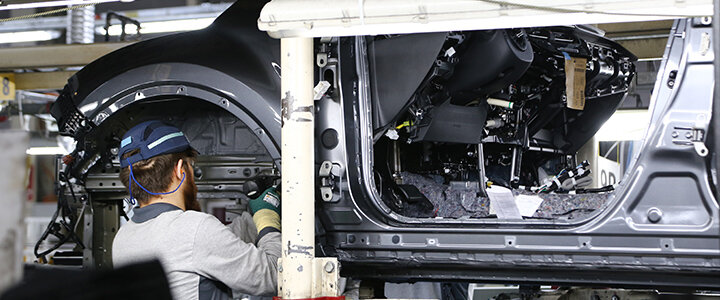
プロファイル
企業 | 海外 自動車製造メーカー |
---|---|
部門 | 複数種類の部品を製造する工場生産企画・管理部門 |
活用状況 | 研究開発部門を中心に、3Dプリンターを活用推進。最終製品への利用にも取り組む3Dプリンター活用先進企業 |
事例概要
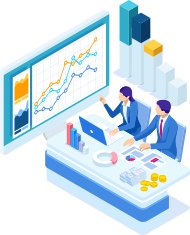
- 3万点以上のパーツから構成される自動車の組み立てや試験には、多くの治具が活用されています。
- 自動車の生産ラインでは、複数の作業員によって組み立てや検査を経ていきます。その際に多くの作業者が同じ基準で組み立てや検査を行う事ができるように、各工程にあわせた治具を用意し、作業の標準化とQCDの維持、向上に貢献しています。
- 例えば自動車のエンブレムなど、完成車両への意匠性の高いパーツの取り付けは作業に気を使う工程の一つです。またこうした組み立てが正しく行われているかを検査する工程でも治具が使われています。
- こうした治具は治具製造業者に発注して用意していく事が多いのですが、作業員の増減や工程の変更に伴う変更のたびに、作り直すことも多く、作業準備期間やコストの面で多くの改善余地が残されていました。
- 治具を社内で設計し、造形を製造現場で行うことで、治具制作にかかるコストを削減するだけではなく、リードタイムを削減し、 よりスピーディーな現場改善に役立てることができます。
従来はどんな課題があったのですか︖
組立は熟練工の勘にたよらず治具で標準化が必要
部品と部品を組み立てた際に、所定の基準を満たしているかを熟練工の経験と勘で判断するのではなく、部品間の位置が正しいかどうかなど、明確に基準を定め、治具を用いて標準化することが重要です。
エンブレムの取り付け作業には、正確な位置決めが求められるため、治具が利用していますが、作業する人員も多く、複数の同一治具が使われていました。
仕様変更のたびに治具変更が必要になりコストと納期が課題
特別使用車やマイナーチェンジなどの仕様改訂のたびに、エンブレム取り付け位治具を改修、または新規に制作する必要がありました。
治具制作業者に発注する以外の方法がなかった為、コストと納期が課題になっていました。
3Dプリンターでどのように課題を解決されましたか︖
3Dプリンター造形にて内製化
上記エンブレム組付け治具を3Dプリンター造形で内製化することにより、コスト削減と納期短縮を狙いました。
複数部品の一体化の実施
当該治具は複数の部品で構成されていたが、3Dプリンター造形用に、特定部品の一体化の設変(設計変更)し、部品点数の削減を推進し、治具の組み立て工数削減と、組立品質向上を実現しました。
治具の部位により最適な材料を使用
車体と接する部分はゴムライク樹脂で造形し、作業時に力が加わるパーツは硬めの材料で造形するなど実施しました。
軽量化、フルカラーによる取付ミス防止を実現
上記治具の一部の子部品をラティス構造にすることにより、軽量化と3Dプリンターで造形する際の造形時間を抑制しました。また材質以外の面でも、フルカラーで治具を造形できる事から、作業内容に応じて治具の色を変えることも可能で、取り組み作業の取り違えを防ぎ、ヒヤリハットを抑制する効果も期待できます。
全ての作業者が、全く同じ作業を同じようにこなすための標準化は非常に重要な取り組みですが、一度できた標準作業に満足することなく、不良率やスループットの継続監視を行い、一層洗練された標準作業に育てていく事が望ましいといえます。
こうしたカイゼンは小さな作業工程の最適化の積み重ねで実現されますが、その際に治具を現場が企画し具現化できることは、現場のカイゼン推進者にとって大きな助けになります。
3Dプリンターはこうしたオンデマンドなモノづくりで現場のカイゼンを推進する強力なツールとなりました。
3Dプリンター導⼊後の効果はいかがですか︖
数多くの位置決め治具や検査治具などを内製できる体制が整ったことでQCDが改善しました。
また内製を行う際に重要な観点は、こうして企画した治具をやみくもに内製しない事でもあります。いままでできなかった治具の作りこみを現場で行う際には治具施策を現場で複数種類つかってどの形状・サイズ・材質が最適かを検討する。その一方で同じ治具が10個必要なのか、100個必要なのかを検討し、複数治具の量産時には外部のサービスビューロを活用し、現場では他の治具の製造を開始するなど、役割分担も重要になってきます。
こうしたハンドリングに必要な知見も、現場自らが実際に3Dプリンターを導入し、利用していく中で最適な組み合わせが見つかってくるノウハウです。取り組み始める事でいままでできなかったことができるようになったという点が最も大きな導入効果かもしれません。
- 解決した製品/サービスはこちら
-
-
カラー樹脂とゴムライク樹脂や透明樹脂をミックスさせると硬さや透明度の調整が可能となり、幅広い用途で使用が可能に。
-
Why RICOH
(リコーだからできる事)
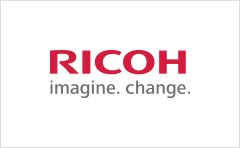
リコーは3Dプリンターをものづくりの現場で20年以上にわたって活用してきました。
製品の試作に始まり治具製造、さらには最終製品製造へと適用範囲を広げております。
2014年以降、自社で蓄積してきたノウハウを活かして
3Dプリンターの販売や3Dプリンター出力サービスを提供しております。
3Dプリンター出力サービスでは、お客様のご要望やご予算に合わせて
最適な造形材料・造形方式・後加工などをご提案しています。
従来の加工方法(切削/射出成型など)とは異なる、
3Dプリントの特性を最大限に活かした造形を丁寧にご支援します。